精密加工における材質選びの重要性とその最適解
2025/03/29
精密加工において、材質選びは成功の鍵を握ります。高精度な製品を生産するには、加工中の寸法安定性や耐久性を考慮した材料選定が必須です。例えば、航空機や医療機器では、軽量でありながら強度の高いチタンやアルミニウムが重宝されます。また、耐熱性や耐腐食性も重要なポイントです。最適な材質選びが、加工の効率化と品質向上を可能にします。
目次
精密加工における材質選びの基本とは
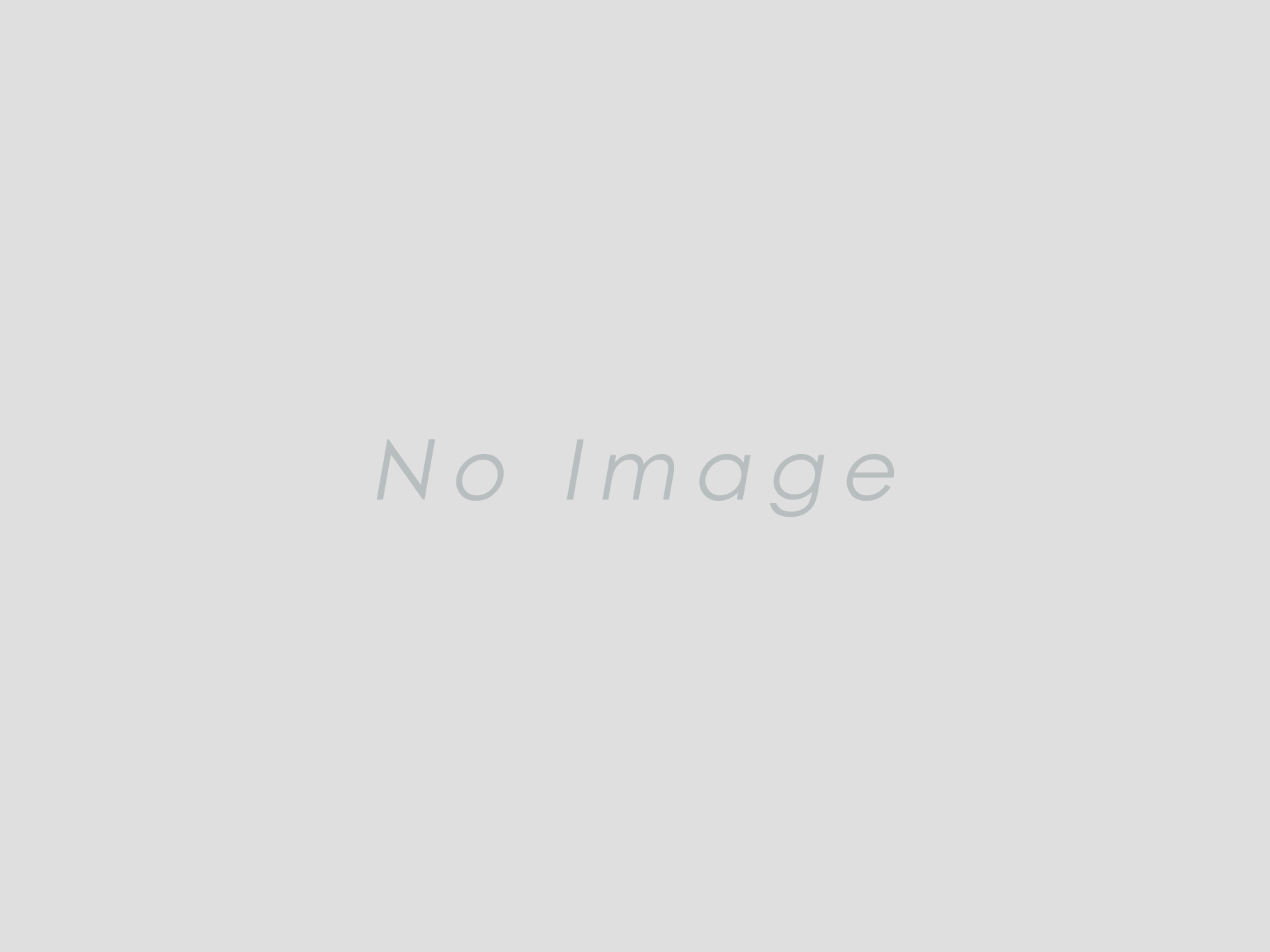
精密加工に求められる材質の基本要素
精密加工における材質選びは、製品の性能と耐久性を左右します。まず、材質の硬度は重要な要素です。硬度が高ければ、耐摩耗性が向上し、加工中の寸法安定性が確保されます。次に、耐熱性は高温環境での加工において不可欠で、特に航空機や自動車部品などで求められます。さらに、耐食性も重要で、これにより製品の長寿命化が図れます。これらの基本要素を考慮し、最適な材質を選定することで、精密加工の品質を向上させることが可能です。
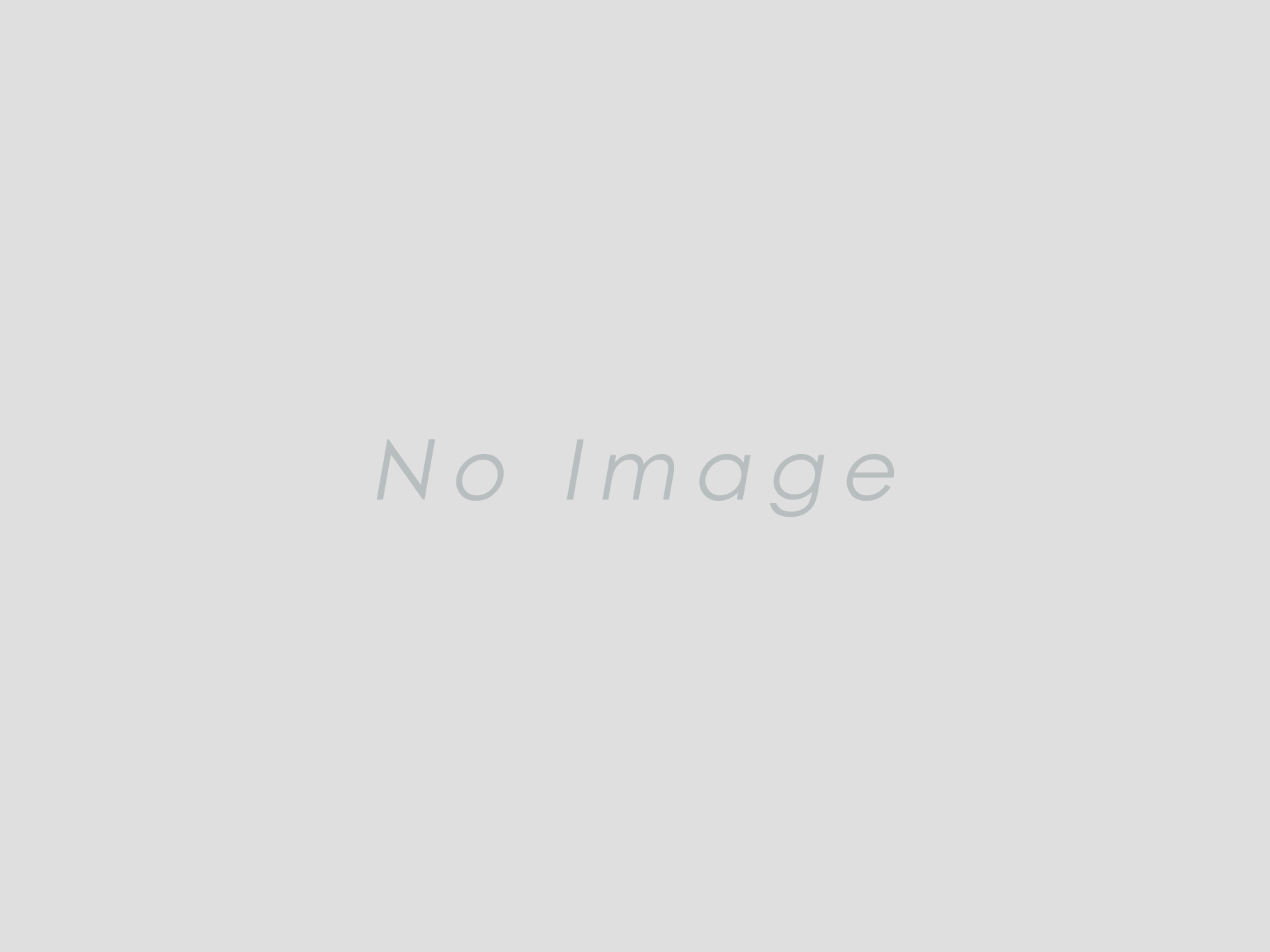
材料の硬度と精密加工の関係
材料の硬度は、精密加工の成否に直接影響を与える重要な要素です。硬度が高い材料は、加工中の刃具摩耗を抑え、より高精度な加工を実現できます。一方で、硬度が高すぎると切削抵抗が増し、加工速度が低下する可能性もあります。そのため、適度な硬度を持つ材料を選び、加工条件に合わせた工具を使用することが求められます。また、硬度とともに、材料の微細構造も重要で、均一な構造は安定した加工品質を保証します。
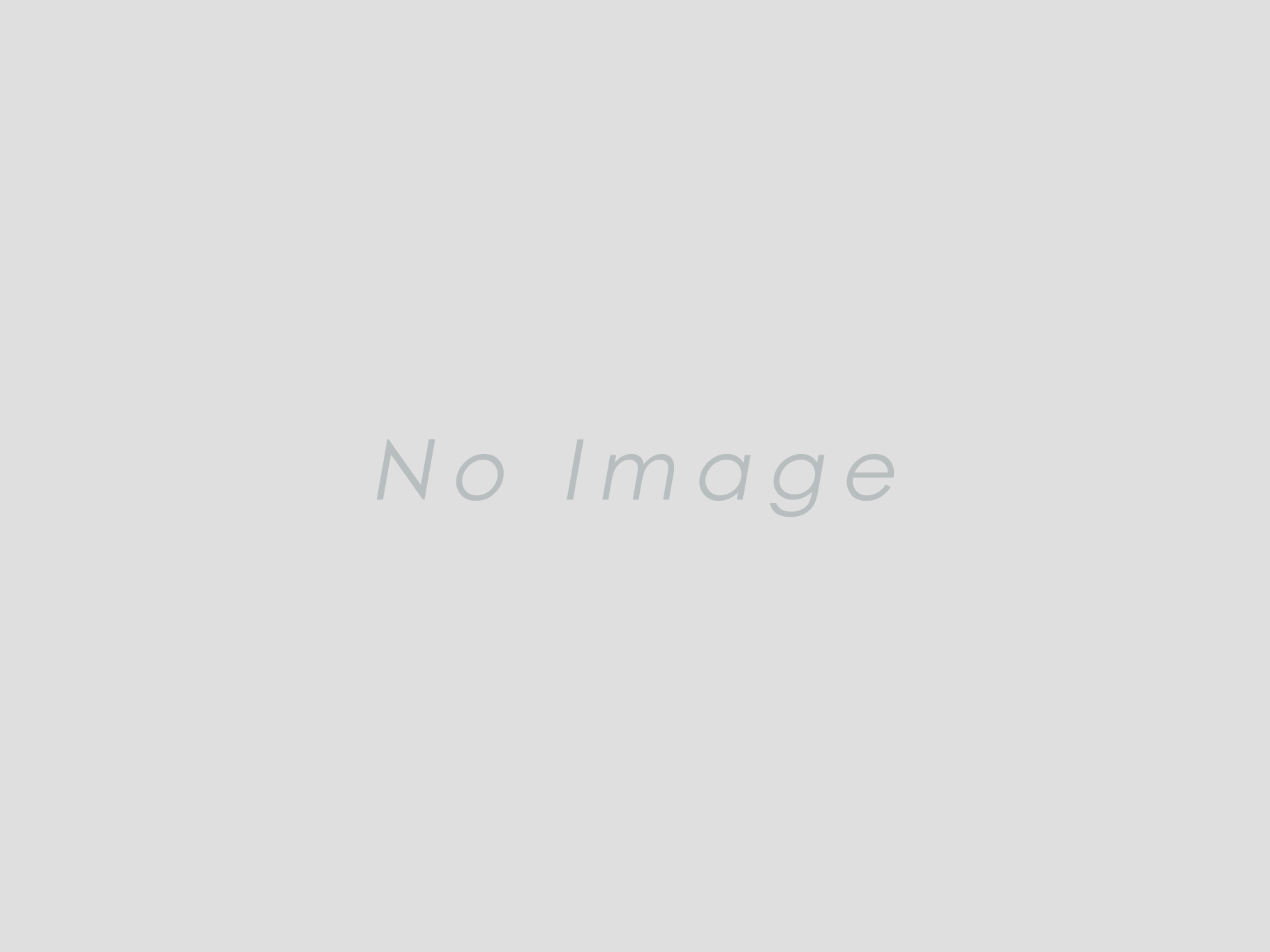
熱処理性が加工結果に与える影響
精密加工において、材料の熱処理性は非常に重要な要素となります。これは、加工中に生じる熱によって材料の特性が変化する可能性があるためです。例えば、鉄や鋼などの金属は、熱処理によって硬度や耐久性が大きく変わります。適切な熱処理は、寸法安定性を保ち、高精度な仕上がりを実現するために不可欠です。また、熱処理を行うことで、材料の内部応力を解消し、加工中の歪みを最小限に抑えることができます。しかし、過度な熱処理は逆に素材を脆くする可能性があるため、十分な検討が必要です。各材料の熱処理性を理解し、適切に管理することが、精密加工の成功に直結します。
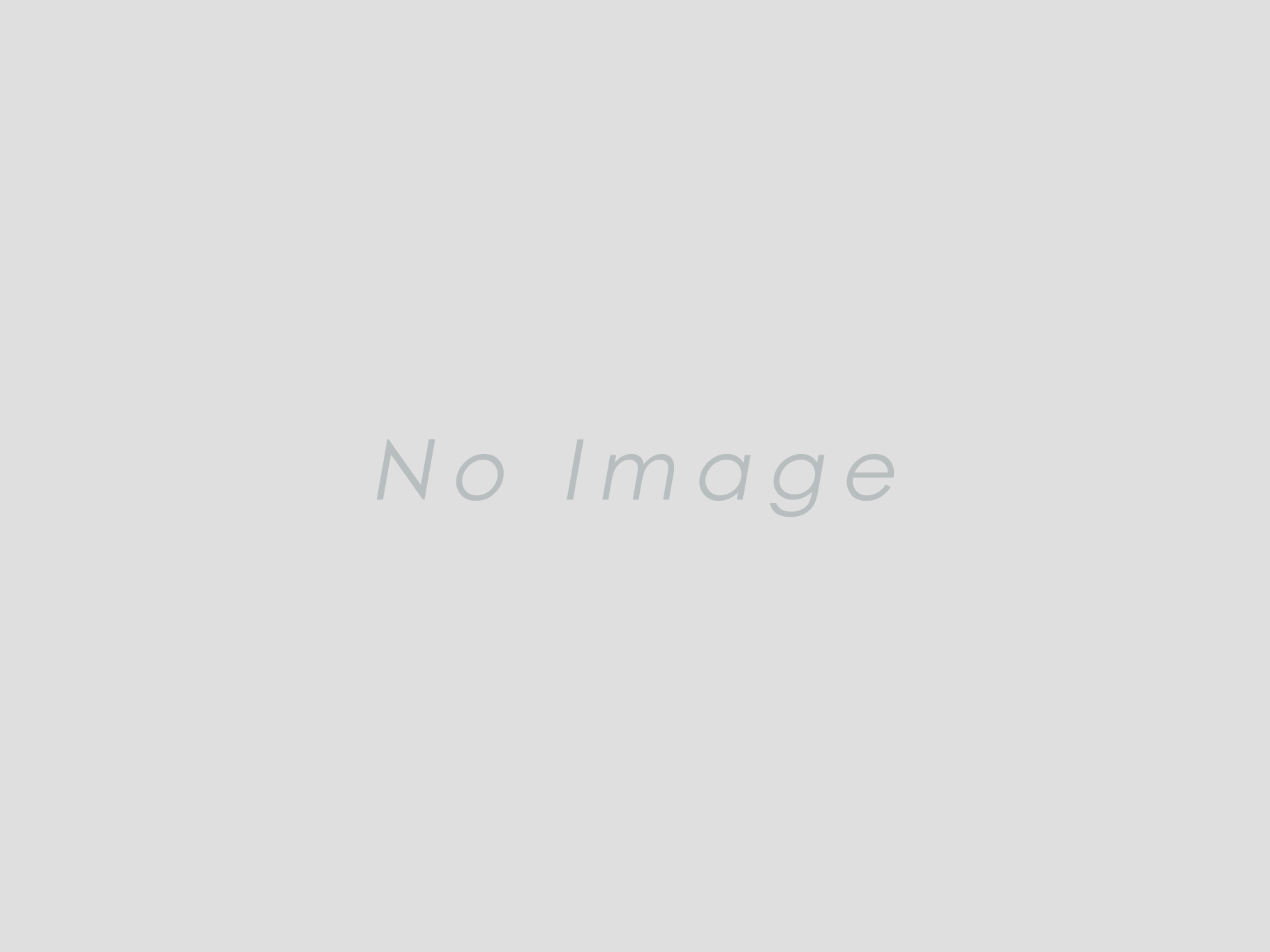
切削性を考慮した材料選択のポイント
精密加工において、切削性を考慮した材料選択は加工効率と品質向上の鍵となります。切削性の良い材料は、加工中の摩耗を減らし、工具寿命を延ばすことができます。例えば、アルミニウムや銅は比較的切削性が良く、加工が容易です。一方、チタンやステンレス鋼は切削性が低く、加工には専門的な技術と工具が必要です。使用する工具や切削速度、そして冷却液の選定は、加工精度に大きな影響を与えます。さらに、切削性が加工コストにも影響を及ぼすため、経済的な観点からも慎重に検討することが求められます。これらのポイントを踏まえた材料選択が、高精度な加工の基盤を築くのです。
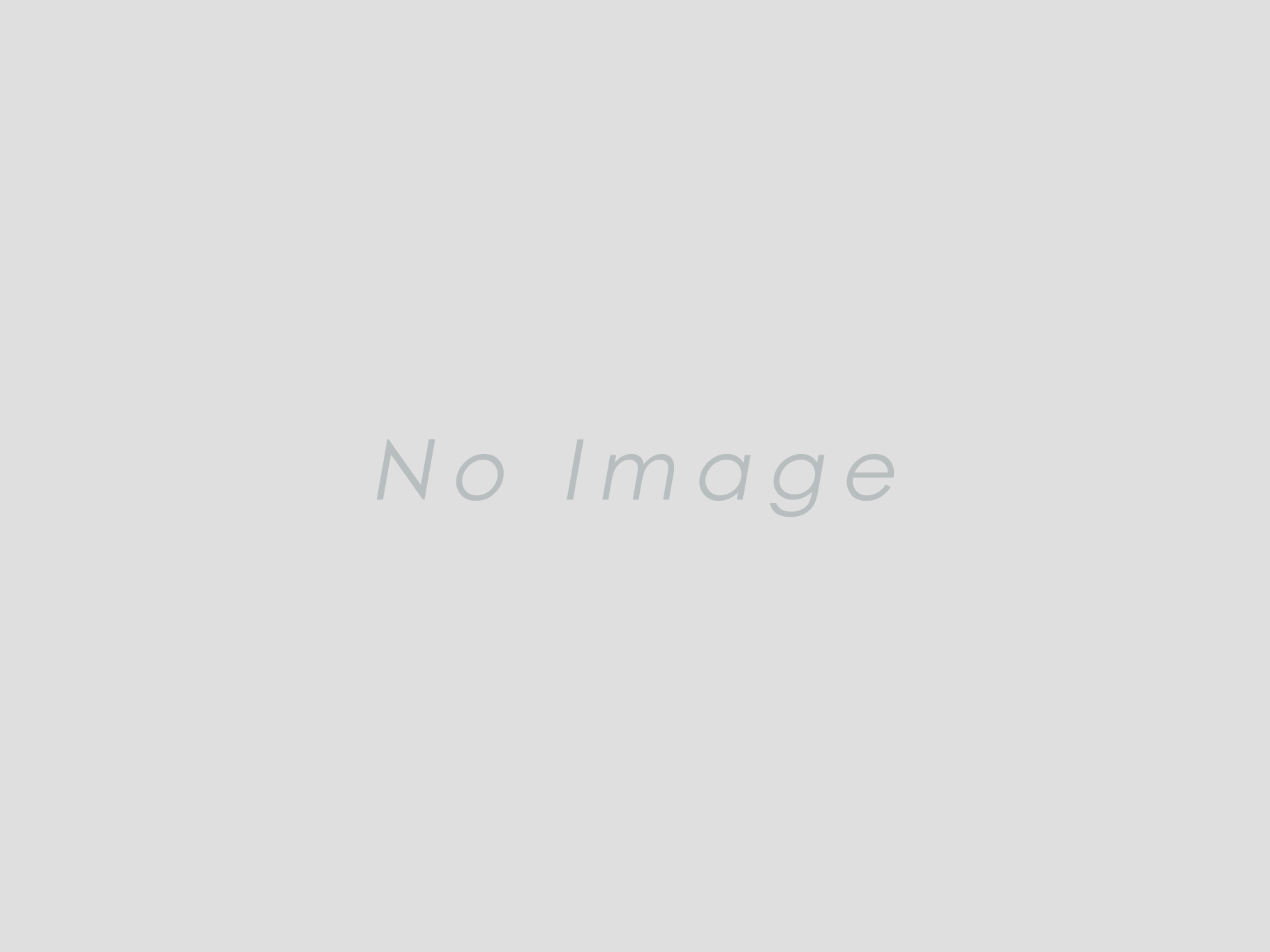
コストパフォーマンスから見る材質選び
精密加工において、コストパフォーマンスは材質選びの重要な要素の一つです。特に、大規模なプロジェクトでは、初期コストと長期的な運用コストを総合的に考慮することが求められます。例えば、耐摩耗性や耐腐食性に優れた材料は、初期投資が高い場合でも、メンテナンス費用を削減し、結果的にはトータルコストを抑えることができます。また、加工性も無視できないポイントです。加工が容易な材質は、製造プロセスを効率化し、不良品の発生を抑えることができるため、結果としてコストパフォーマンスが向上します。このように、材質の選定は多角的な視点から行う必要があり、最適な選定を行うことでプロジェクト全体の費用対効果を最大化することが可能です。
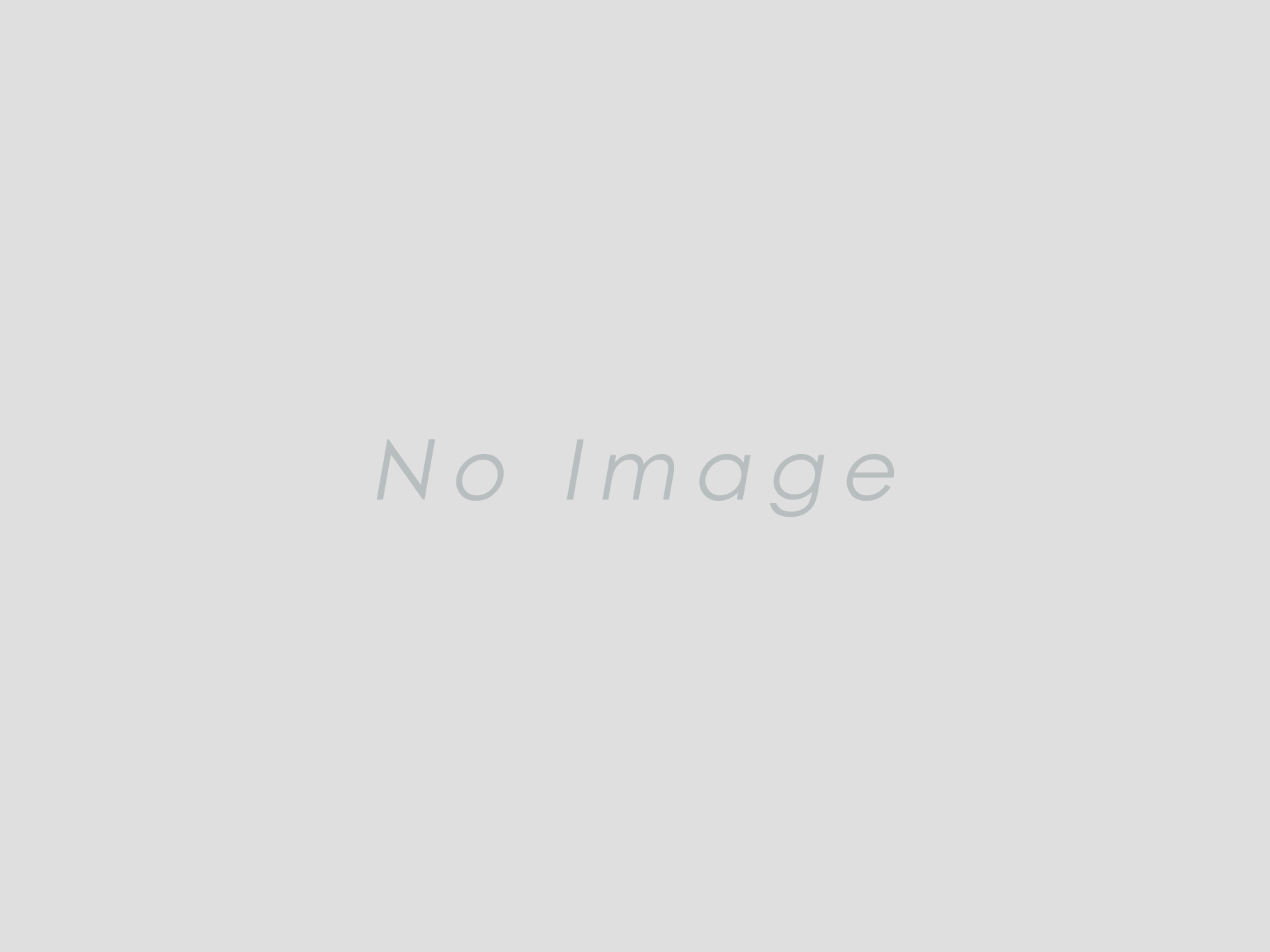
環境に優しい材料選びの重要性
近年、環境に優しい材料選びが精密加工において重要性を増しています。持続可能な開発を目指す上で、環境負荷を低減する素材の選定は企業として避けて通れない課題です。リサイクル可能な材料や、製造過程でのCO2排出量が少ない材料を選ぶことで、環境への影響を最小限に抑えることができます。さらに、環境に配慮した材料は、企業の社会的責任を果たす意味でも重要です。消費者の環境意識が高まる中、エコフレンドリーな製品は市場での競争力を高める要素となります。したがって、環境に優しい材料選びは、精密加工における経済的利益と社会的価値を両立させるための重要なステップであり、今後ますます注目されることでしょう。
材質の特性が精密加工に与える影響を深掘り
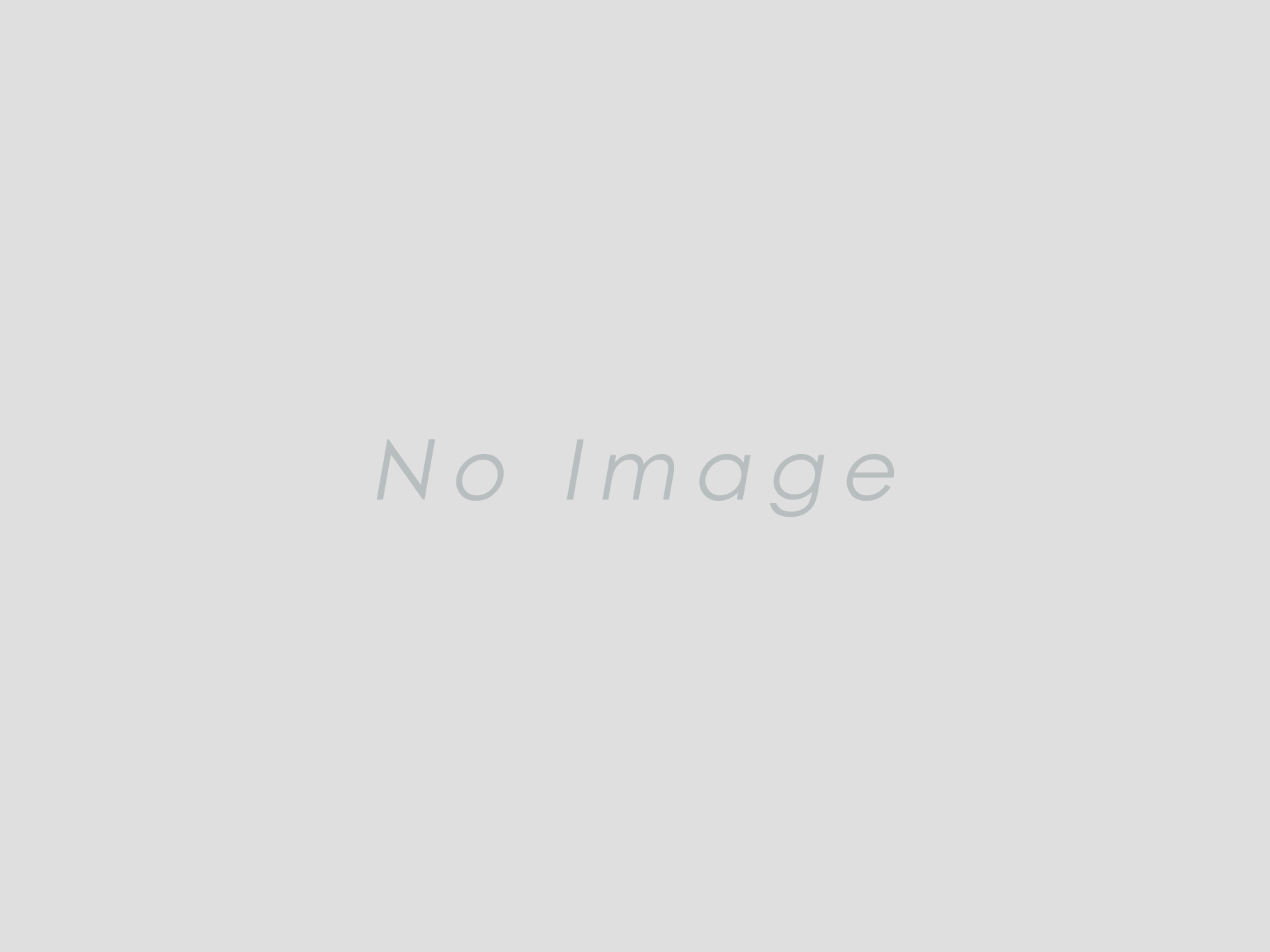
寸法安定性が精密加工に与える影響
精密加工において、寸法安定性は極めて重要な要素です。材料が加工中に温度や応力の変化に対してどれだけ形状を保つことができるかは、製品の品質に直結します。例えば、航空機産業では、部品が微小な変形を起こしただけでも大きな問題となります。そのため、寸法安定性に優れた材料の選定が不可欠です。精密加工で用いられる工具鋼や高炭素鋼は、寸法安定性が高く、加工精度向上に貢献します。これにより、最終製品の品質を確保し、高精度な製品の提供が可能となります。寸法安定性を考慮した材料選びは、加工効率の向上と品質の安定に寄与するため、慎重な選定が求められます。
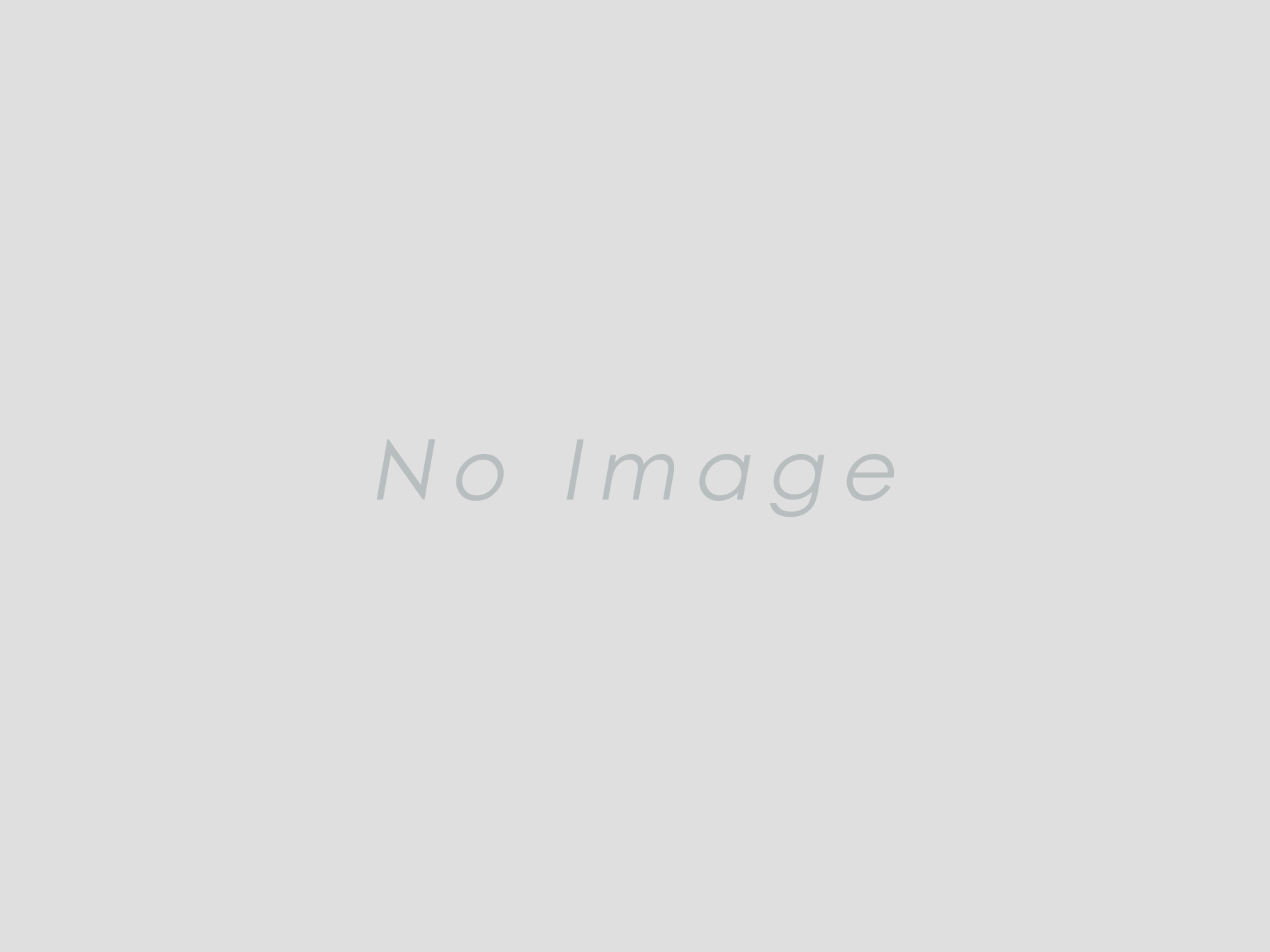
材料特性による加工精度の違い
精密加工における加工精度は、選択する材料の特性に大きく依存します。硬度や耐摩耗性の異なる材料は、加工中に異なる反応を示し、これが加工精度に影響を及ぼします。例えば、チタンは軽量で強度があるため、航空宇宙や医療分野で重宝されますが、その硬度ゆえに加工時の工具摩耗や熱発生を考慮しなければなりません。一方、アルミニウムは加工が容易で、高速加工が可能ですが、寸法の安定性や耐久性に注意が必要です。これらの特性を考慮に入れ、適切な加工方法と組み合わせることで、精密加工の精度を最大化することができます。最適な材料選びは、加工の成功に直結するため、詳細な特性分析と慎重な選定が必要です。
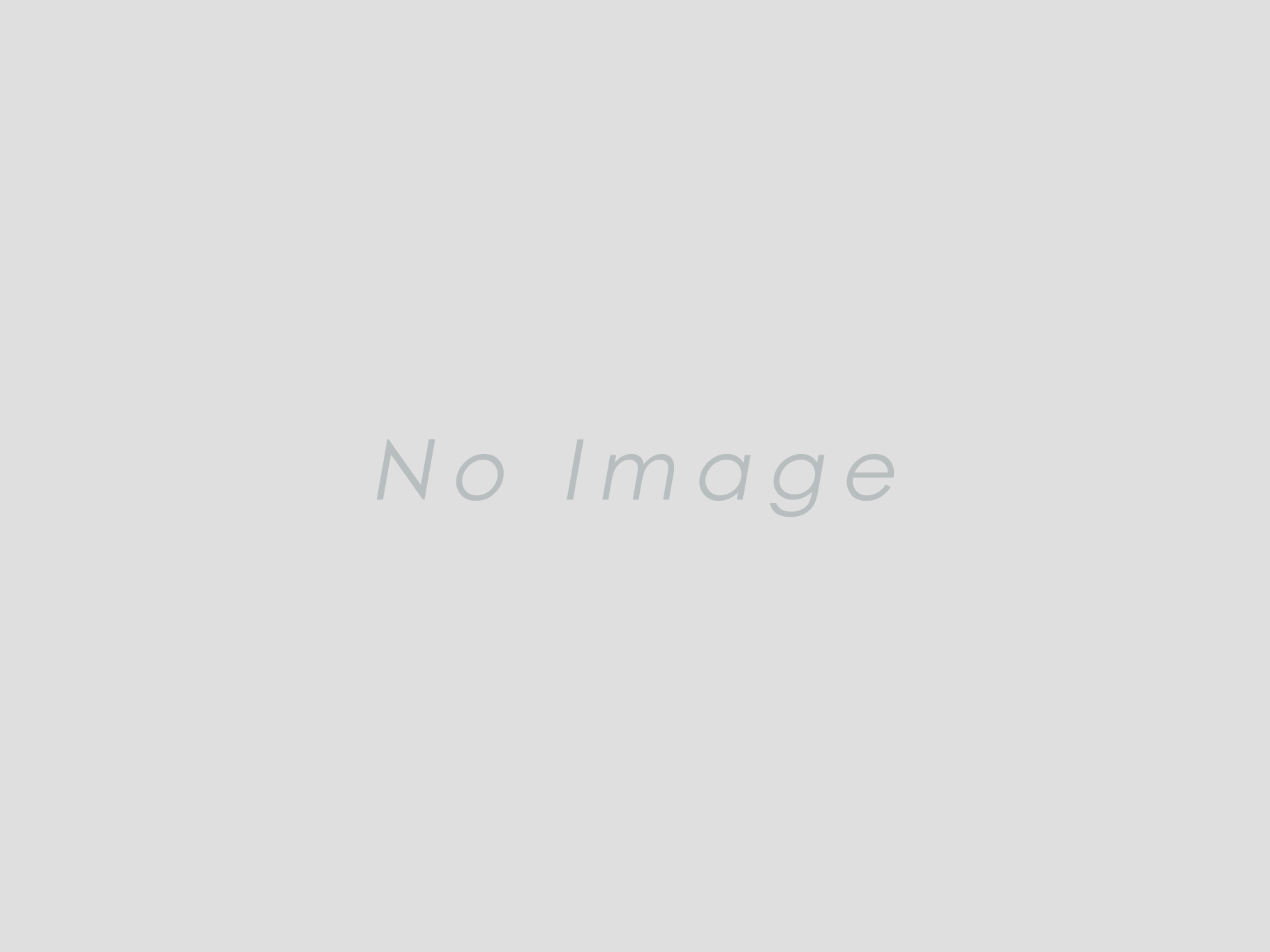
耐摩耗性がもたらす加工効率の向上
精密加工において、耐摩耗性の高い材料を選ぶことは加工効率の向上に直接つながります。例えば、工具の寿命を延ばすために超硬合金やセラミックを使用することが一般的です。これにより、工具の交換頻度が減り、加工の中断を最小限に抑えることが可能です。さらに、耐摩耗性の高い材料は摩擦を減少させることで、加工速度を向上させる効果もあります。セラミックの例では、熱伝導率が高く、加工中の熱を効率的に逃がすことで、熱変形を防ぎます。これにより、加工精度が向上し、精密な製品を安定して生産することが可能となります。耐摩耗性を考慮した材料選びは、製品の品質向上と加工コストの削減に大きく寄与します。
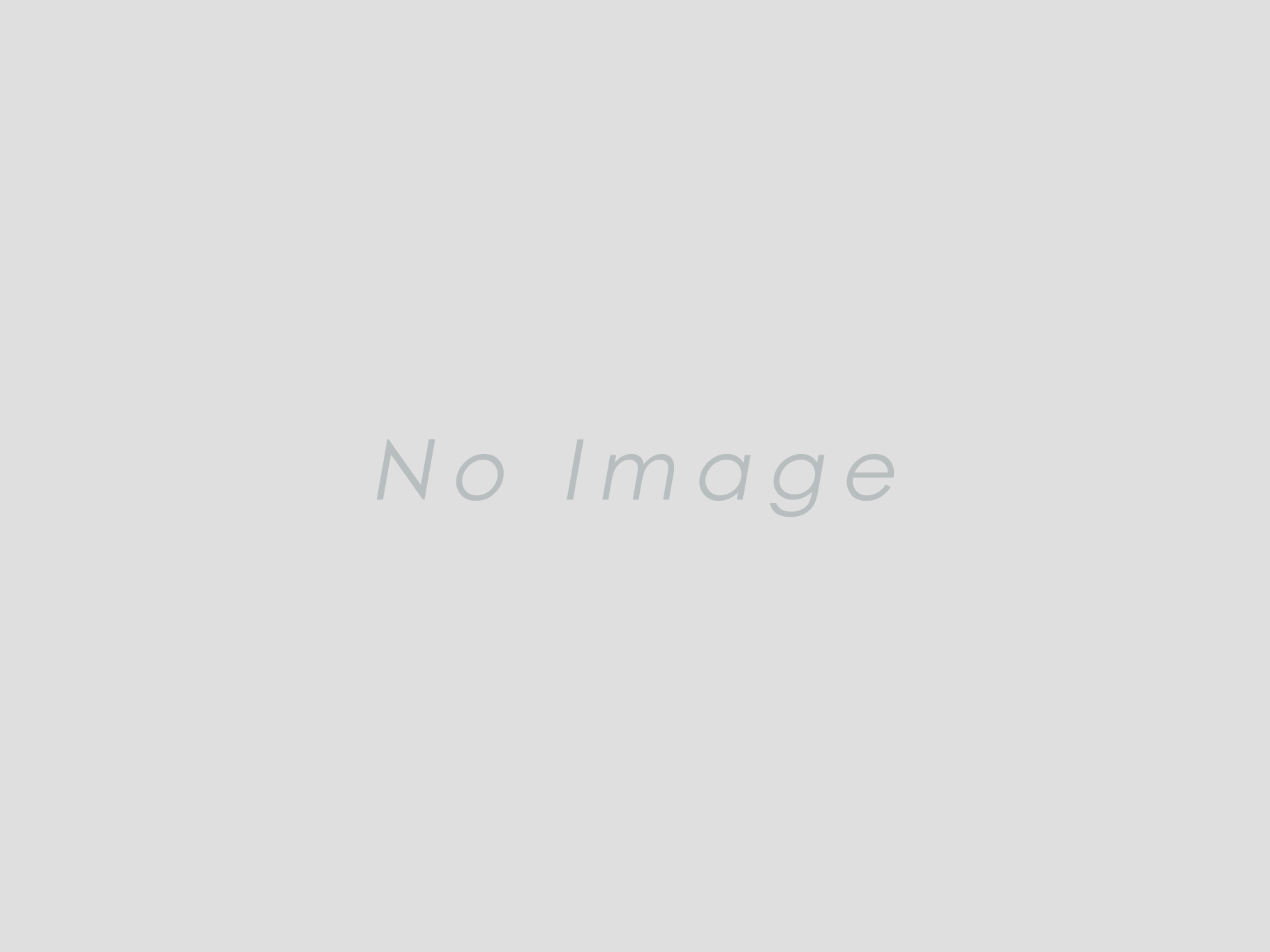
精密加工における熱膨張の考察
精密加工では、熱膨張が加工精度に大きな影響を与える要因の一つです。金属や合金は加工中に発生する熱によって膨張し、寸法誤差を引き起こします。このため、熱膨張係数の小さい材料を選ぶことが重要です。特に航空機や宇宙機器の部品では、微細な寸法変化でも大きな影響を及ぼすため、熱膨張を抑制するための材料選定が欠かせません。また、冷却技術や加工速度の最適化も重要です。例えば、加工中の冷却剤の適切な選定と使用により、熱の影響を最小限に抑えることができます。これにより、精度を保ちつつ効率的な加工を実現することが可能となります。熱膨張の影響を理解し、適切な対策を講じることで、精密加工の成功を左右する重要な要素を管理することができます。
航空機や医療機器に適した精密加工用材質
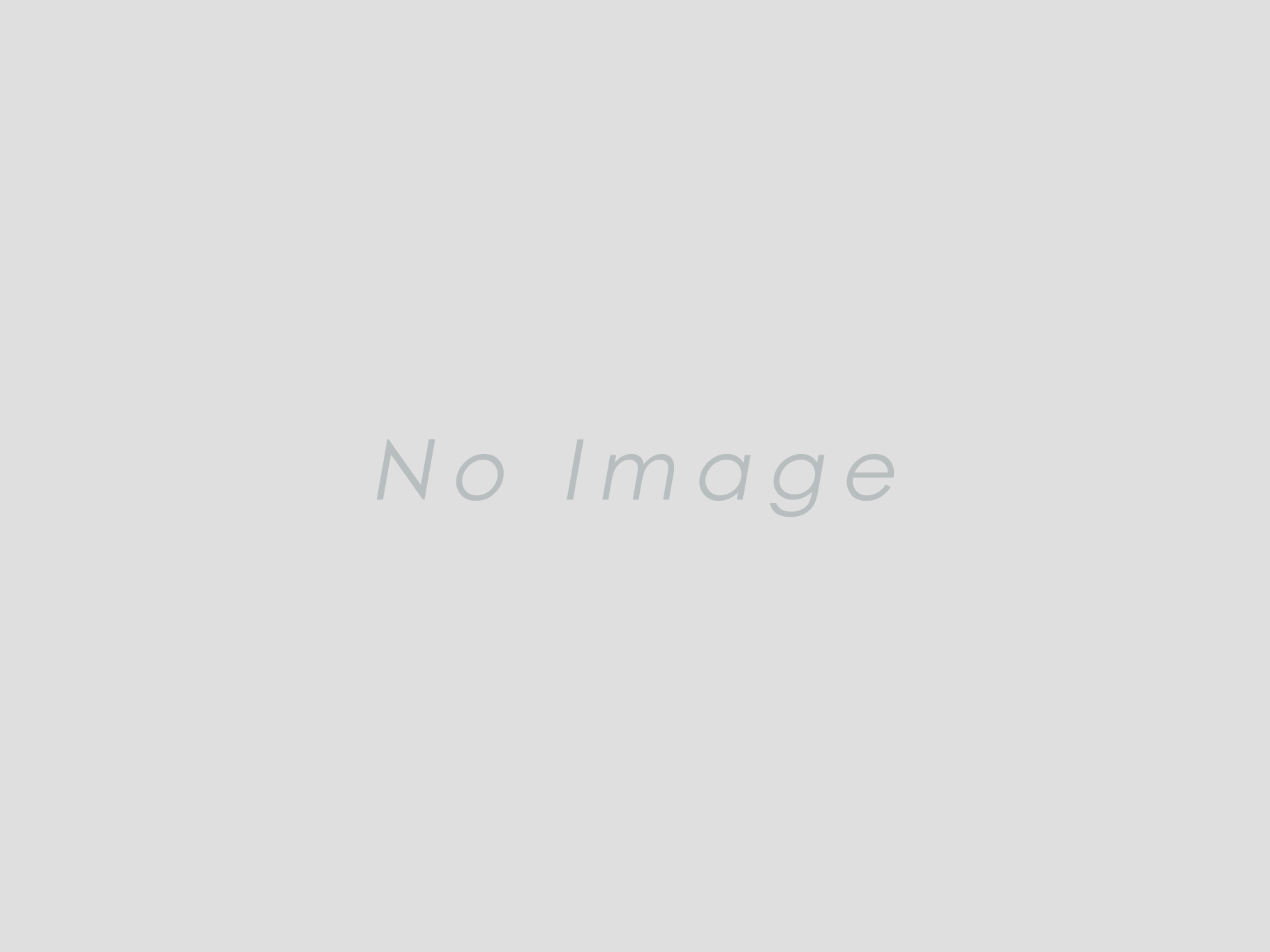
航空機に求められる軽量材質とは
航空機産業では、軽量でありながら高い強度を持つ材料の選定が重要です。特に、チタンやアルミニウム合金が広く採用されています。チタンはその優れた強度と耐腐食性から、機体の構造部材やエンジン部品に使用され、その軽量性は飛行性能の向上に直結します。一方で、アルミニウム合金は加工性に優れ、機体の一部に使用されることで、全体の軽量化に貢献します。これらの素材選びは、飛行の効率性を高め、燃料消費の削減や航続距離の延長に寄与します。また、これにより航空機の運用コストを抑えつつ、安全性を確保することができます。
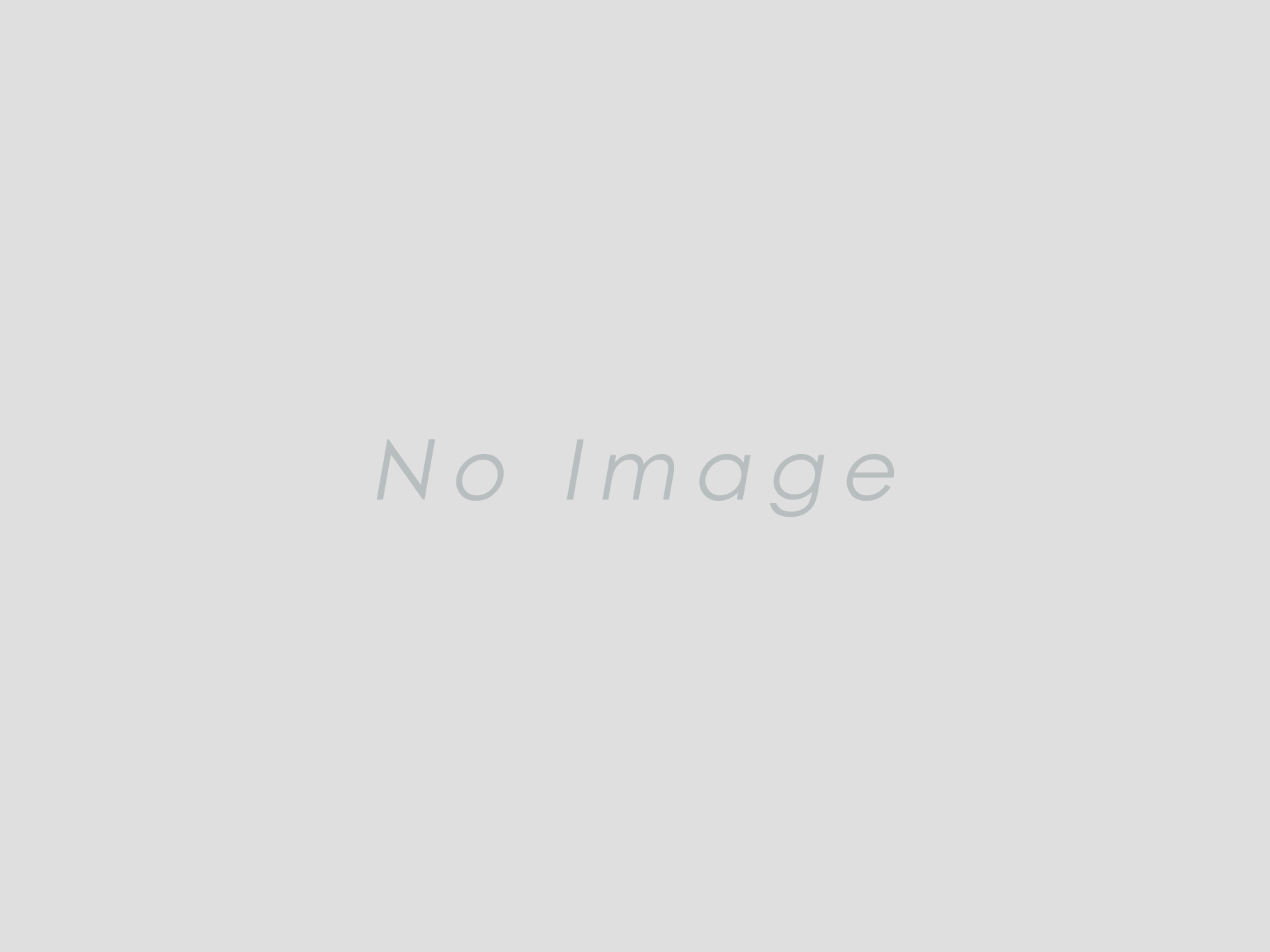
医療機器に最適な生体適合性材料
医療機器において、生体適合性材料の選定は患者の安全性と治療結果に直接影響を与えます。精密加工における材質選びでは、長期間体内に留まるインプラントや、短期間使用されるデバイスの双方で生体適合性が求められます。チタンはその優れた生体適合性と強度から、人工関節や歯科インプラントに採用されることが多いです。これに対し、ポリウレタンなどの高分子材料も、カテーテルや心臓ペースメーカーの外装に使用され、その柔軟性と耐久性が評価されています。このように、医療機器の材質選びでは、生体との長期的な相性と耐久性を重視した選定が重要です。
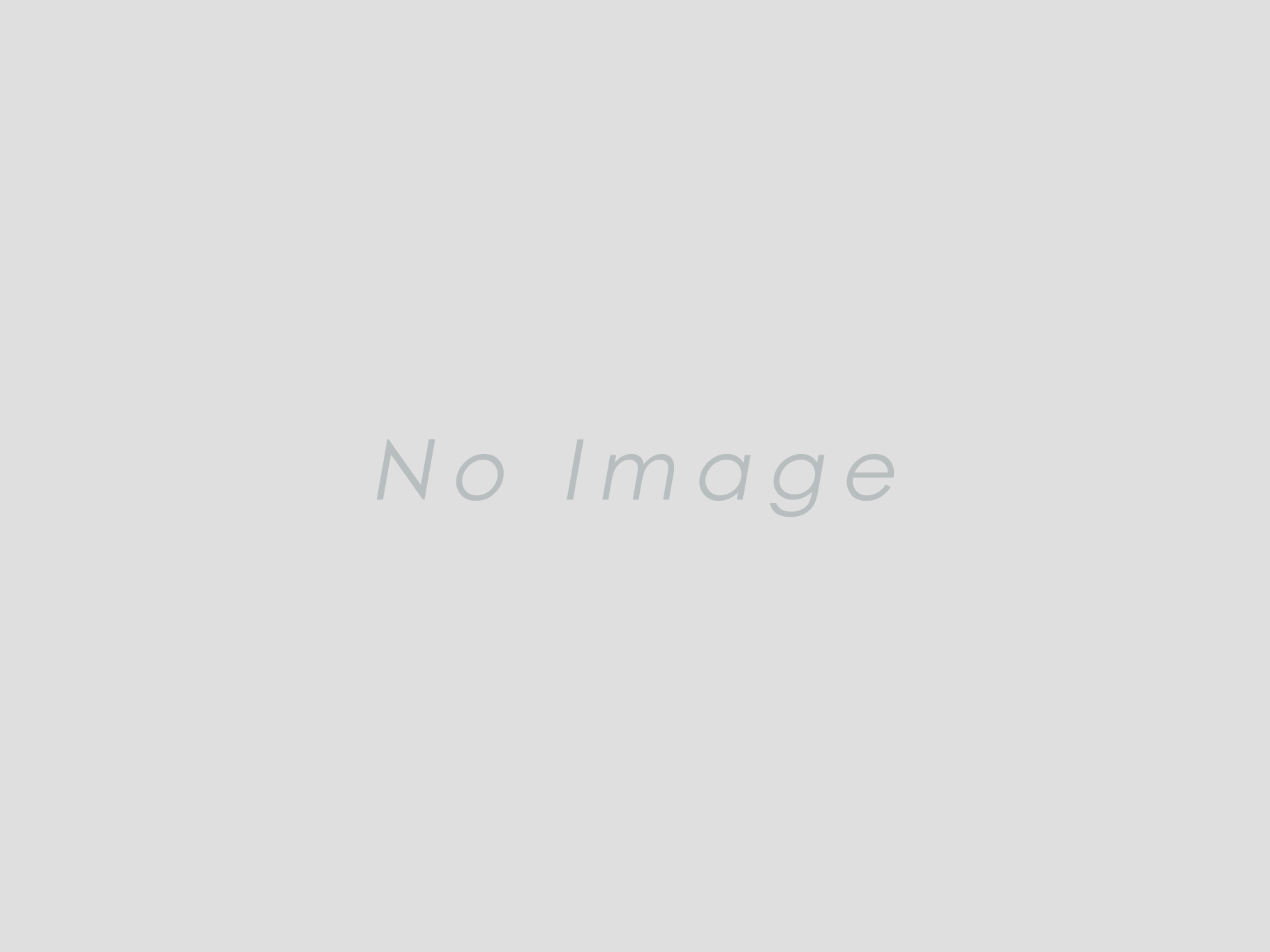
チタンの特性とその応用
チタンは精密加工において非常に重要な材質の一つです。その特性として、軽量でありながら強度が高いことが挙げられます。具体的には、チタンはアルミニウムの約60%の重量でありながら、同等の強度を実現します。この軽量性と強度の組み合わせにより、航空機部品や宇宙構造物としての応用が進んでいます。また、チタンは耐腐食性にも優れ、海洋構造物や化学プラントでの使用にも適しています。特に、酸や塩水に対する耐性が高く、過酷な環境下でも安定した性能を発揮します。医療分野では、生体親和性が高くアレルギー反応を引き起こしにくいため、人工関節や歯科用インプラントとして利用されています。これらの特性は、精密加工における材質選びの重要性を再認識させるものです。
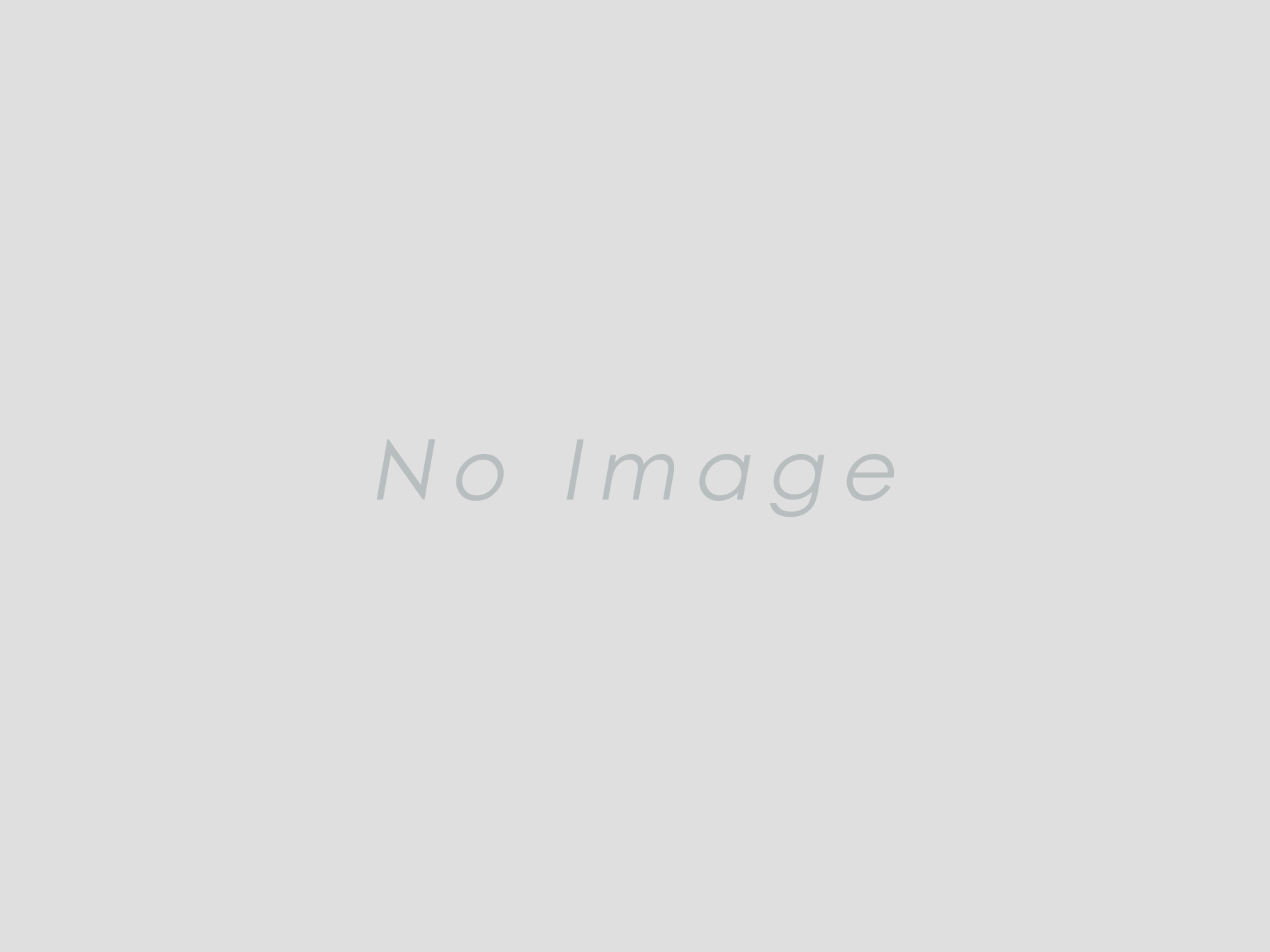
アルミニウムの強度と耐久性
アルミニウムは精密加工において頻繁に選ばれる材質で、その理由としては、軽量で加工が容易であることが挙げられます。アルミニウムは、他の多くの金属と比較して密度が低く、輸送が容易であるため、航空機や自動車の部品として広く採用されています。さらに、アルミニウムは耐食性があるため、外部環境の影響を受けにくく、長期間にわたって信頼性を維持できます。また、リサイクル可能で環境にも優しいため、持続可能な製造プロセスにおいても重要な役割を果たしています。アルミニウムを使用することで、製品の耐久性を維持しつつ、コスト効率を向上させることが可能です。これにより、精密加工における材質選びの最適解を模索する上で、アルミニウムは欠かせない選択肢となっています。
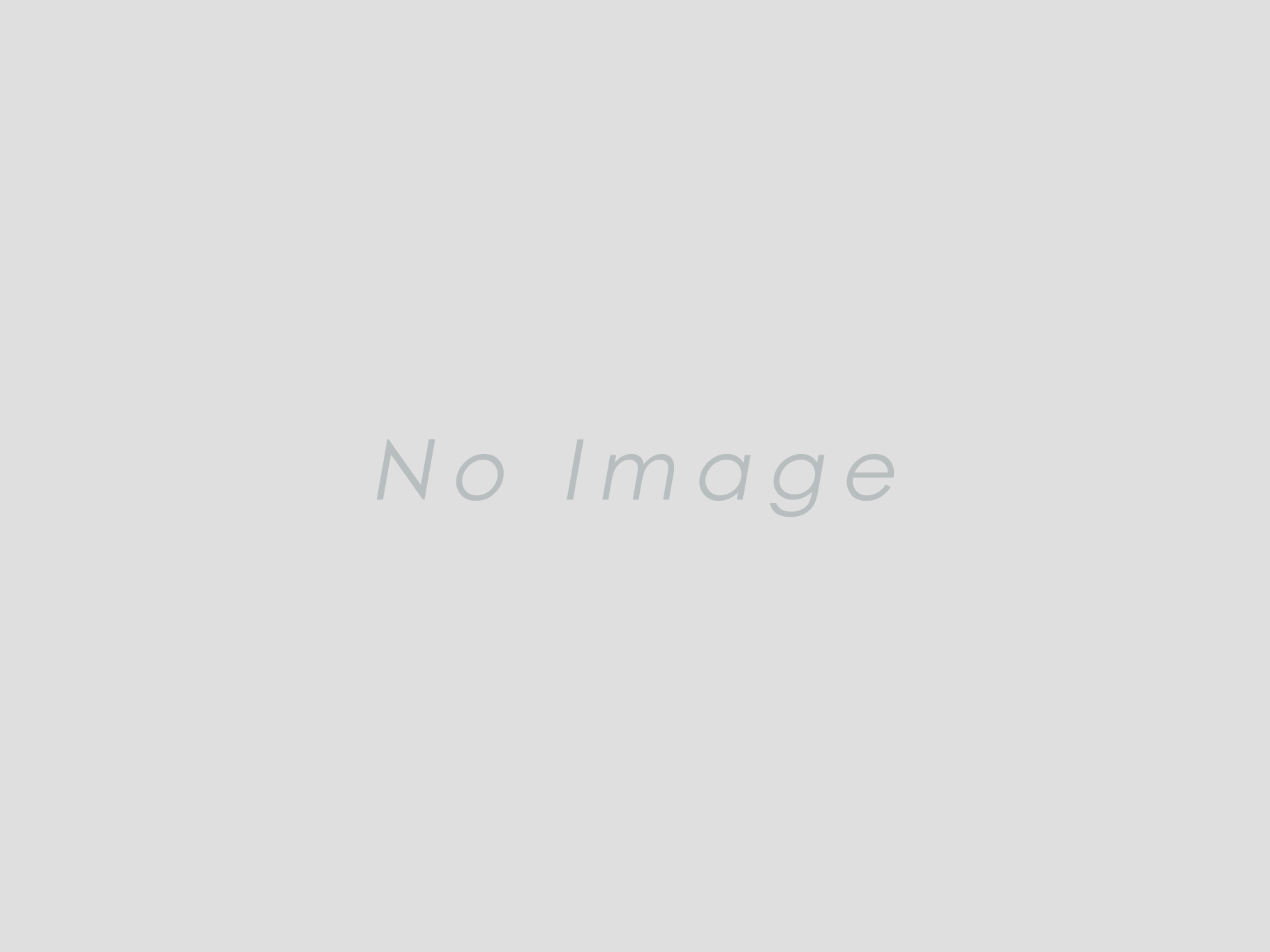
ニッケル合金の耐熱性とその利点
精密加工におけるニッケル合金の活用は、その優れた耐熱性が大きな魅力です。特に高温環境下での使用が求められる航空宇宙分野や化学工業において、この合金は不可欠な存在となっています。ニッケル合金は、800°Cを超える高温でもその形状や特性を維持することができるため、極めて信頼性が高いです。また、耐腐食性に優れているため、過酷な化学環境でも長期間使用が可能です。このような特性により、ニッケル合金は製品の安全性と耐久性を大幅に向上させることができます。さらに、ニッケル合金の加工には専用の高硬度工具が必要ですが、適切な技術を駆使することで、高精度な製品を効率的に生産できる点も大きな利点となっています。
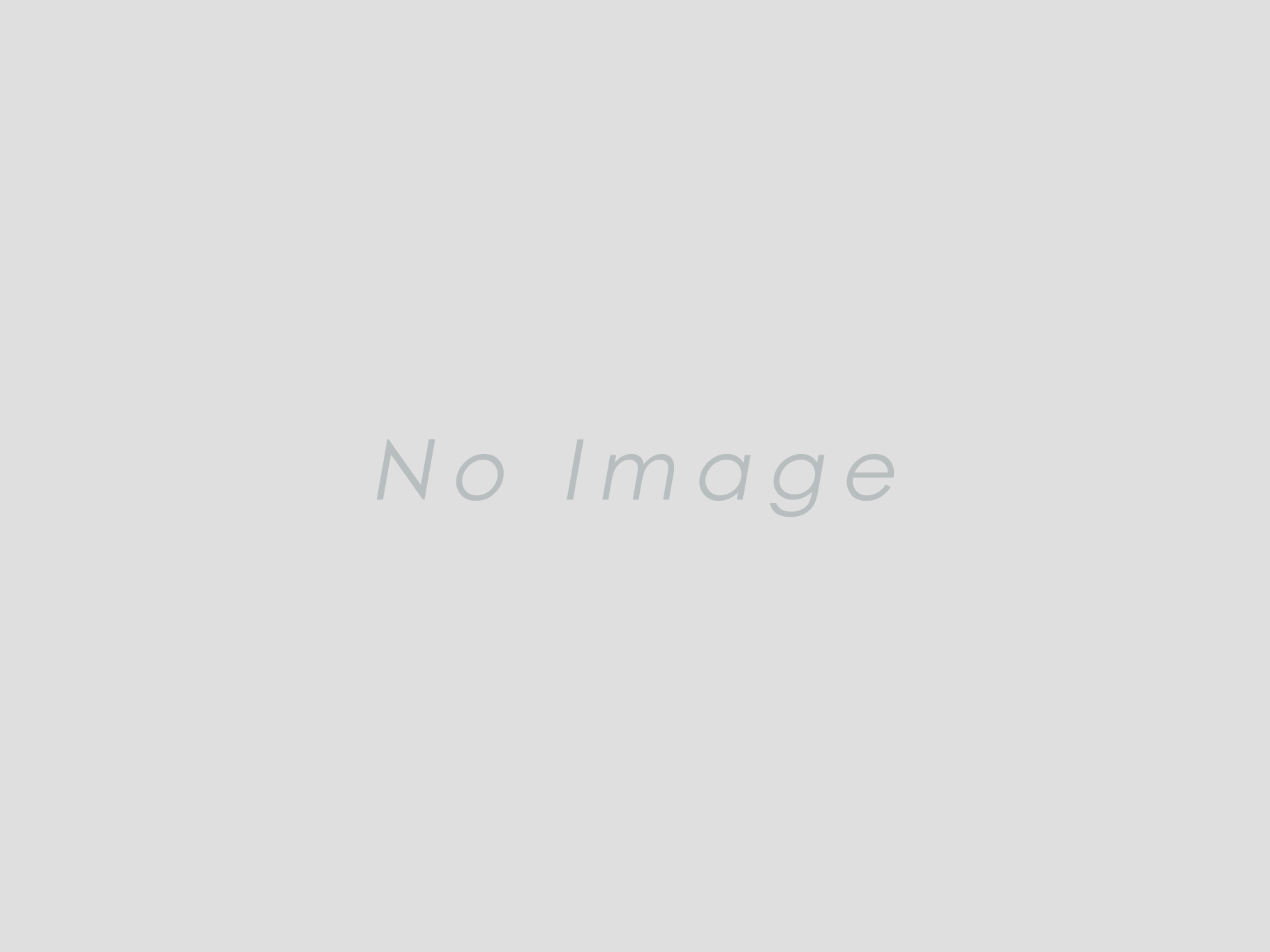
素材の選定がもたらす安全性の向上
精密加工における素材選定は、安全性を高めるための重要な要素です。例えば、航空機や医療機器では、軽量かつ高強度な素材が求められます。軽量化により燃費が向上し、強度が高ければ高い安全性が確保できます。また、生体適合性が要求される医療機器では、生体との相性が良いチタンやアルミニウムが採用されることが多いです。これらの材質は、人体に優しく、腐食や劣化に対する耐久性も兼ね備えています。素材選定の適切さが、機能性のみならず、ユーザーに安心を提供し、信頼性を高めることに繋がります。このように、精密加工における素材選定は、単なる製品性能の向上に留まらず、全体の安全性と信頼性を大幅に向上させる要素となっています。
精密加工で重視すべき耐熱性と耐腐食性の重要性
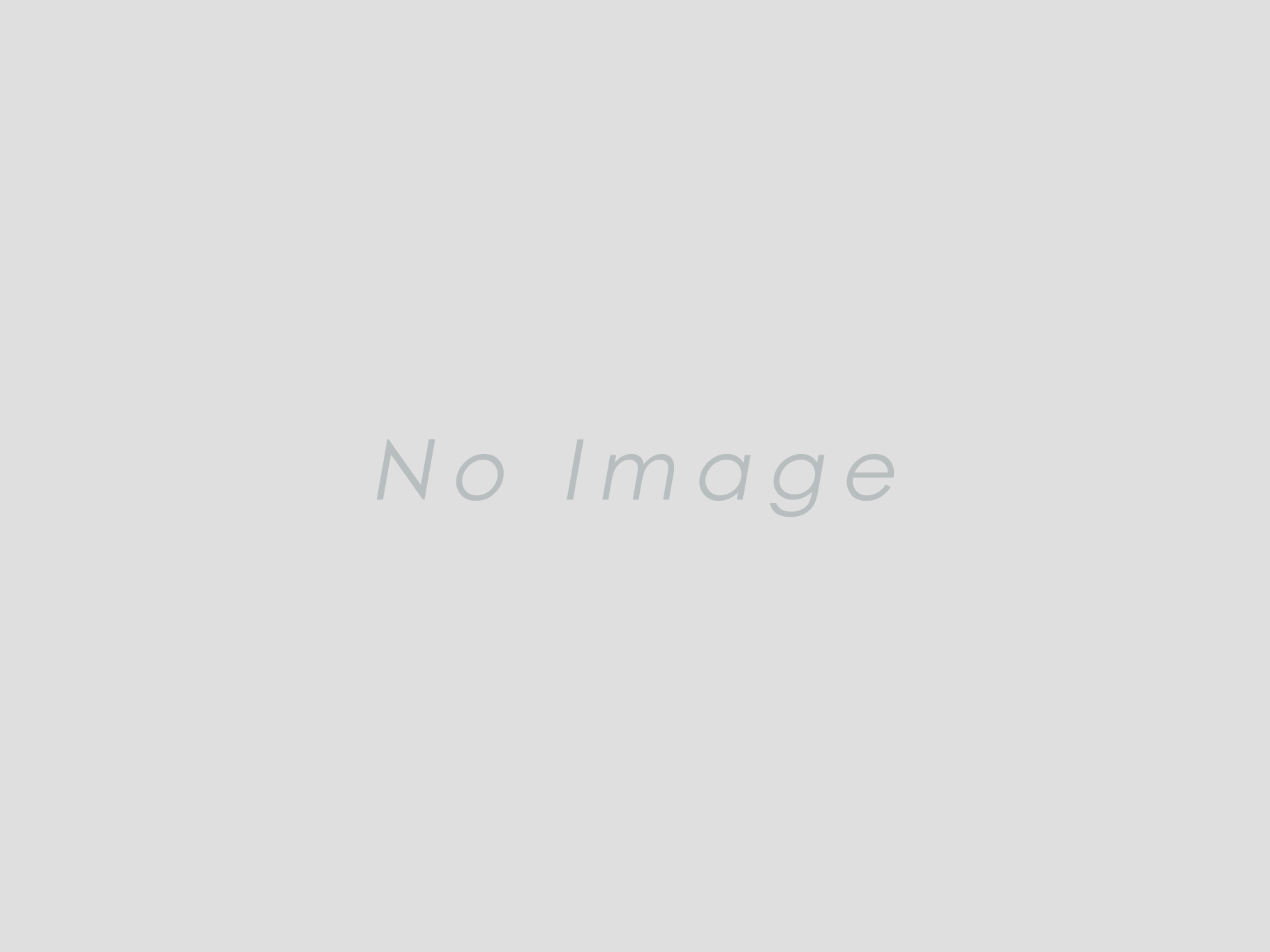
耐熱性が必要な加工環境とは
精密加工において耐熱性が必要な場面は多岐にわたります。特に航空宇宙産業や自動車産業では、熱負荷がかかる環境下でも部品が安定して機能することが求められます。こうした環境では、チタン合金や耐熱ステンレス鋼などの材料が選ばれることが一般的です。これらの材料は高温でも寸法安定性や強度を維持するため、加工時の熱による変形や劣化を最小限に抑えることができます。耐熱性が求められる環境では、単に高温に耐えるだけでなく、熱膨張の影響や熱伝導率も考慮して材料を選定することが重要です。これにより、製品の信頼性を確保し、長期使用における性能の安定性を保証することができます。
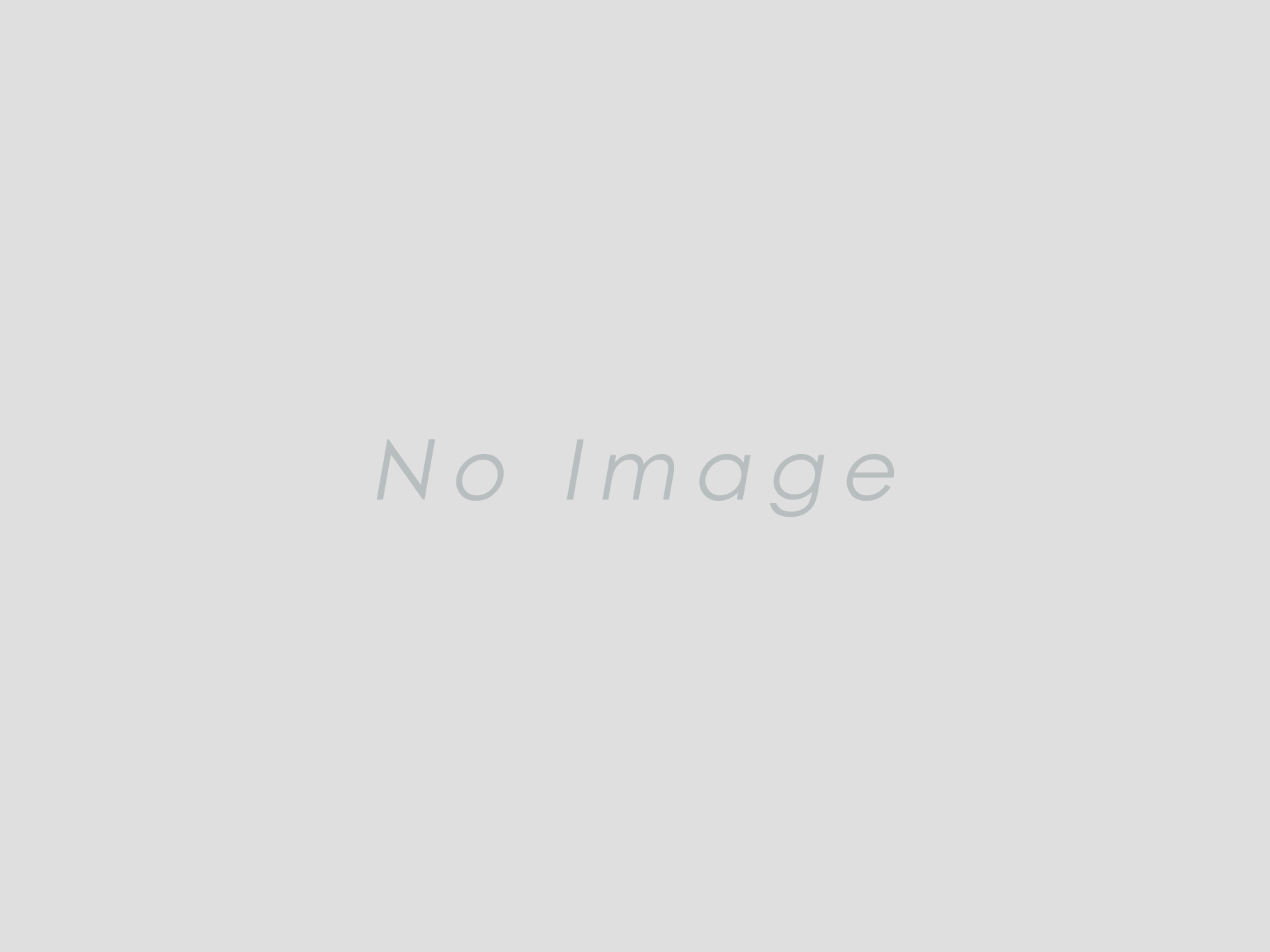
腐食に強い材料の選定基準
腐食に強い材料選びは、精密加工製品の品質と耐久性を左右する重要な要素です。特に医療機器や海洋設備などの腐食性の高い環境では、耐食性が高い材料の使用が必須です。ステンレス鋼のSUS304やSUS316は、その優れた耐食性から広く利用されています。材料選定においては、使用環境の化学的特性や湿度、温度などを詳細に評価し、最適な材料を選ぶことが求められます。さらに、材料の表面処理やコーティングも腐食に対する防御策として考慮されるべきです。これにより、腐食による製品の劣化を防ぎ、維持管理の手間を軽減することが可能となります。
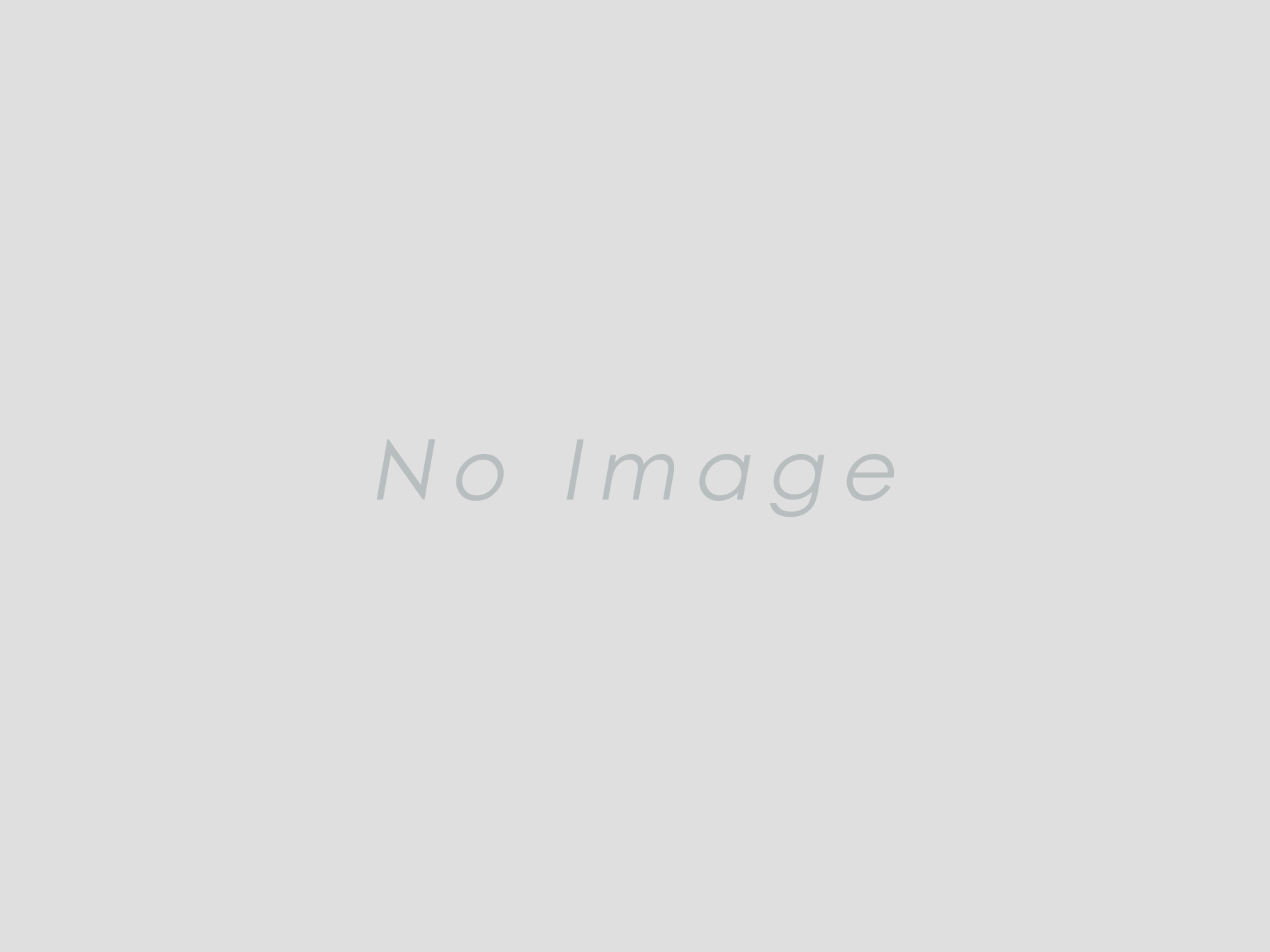
高温環境下での材質選びのポイント
精密加工における高温環境下での材質選びは、製品の性能を左右する重要な要素です。高温では材料の熱膨張、強度の低下、酸化が課題となります。アルミニウムやチタンは優れた強度と軽量性を兼ね備え、熱伝導性も高いため、発熱を効率的に逃がします。また、セラミックや炭素繊維強化プラスチックも耐熱性に優れており、高温環境での寸法安定性を確保します。これにより、精密加工品の高精度維持が可能となります。材質選びでは、使用温度範囲や加工の目的に応じて、最適な素材を選定することが求められます。特に航空機や自動車などの高温環境は、熱に対する耐性が製品寿命に直結するため、材料の選定が非常に重要です。
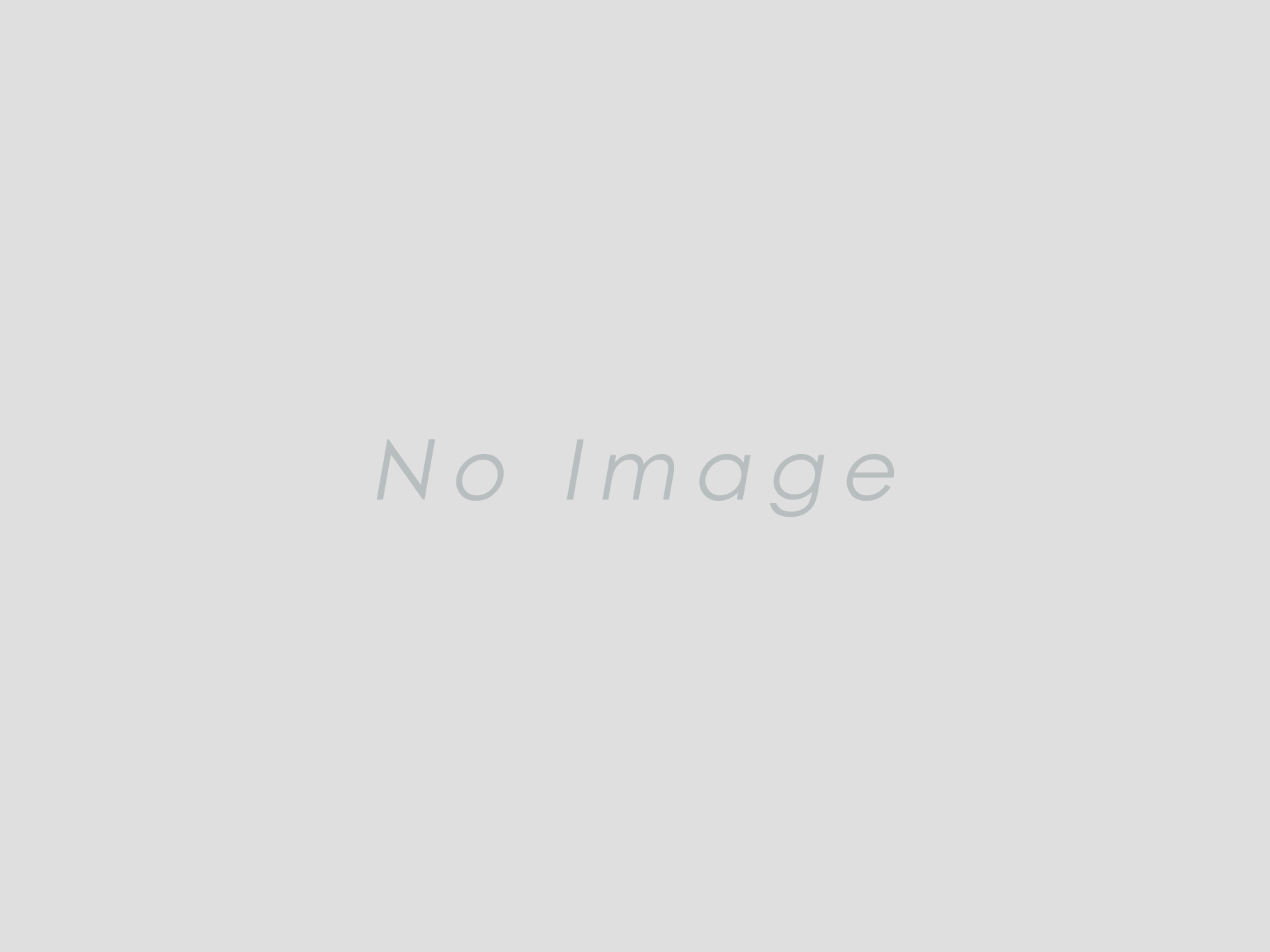
化学反応を防ぐ材料選びの重要性
精密加工において、化学反応を防ぐための材料選びは非常に重要です。特定の環境では、材料が化学反応を起こし、腐食や変形を引き起こすことがあります。このような環境では、ステンレス鋼やニッケル基合金が特に有効です。これらの材料は優れた耐腐食性を持ち、化学薬品や湿度が高い環境でも安定した性能を発揮します。また、プラスチックやゴムなどの非金属材料も、特定の薬品に対して耐性があるため、用途によっては選択肢となります。化学反応を防ぐことは、製品の品質維持と長寿命化に直結します。したがって、使用環境を詳細に分析し、それに応じた最適な材料を選定することが不可欠です。
効率的な精密加工を実現するための材質選定戦略
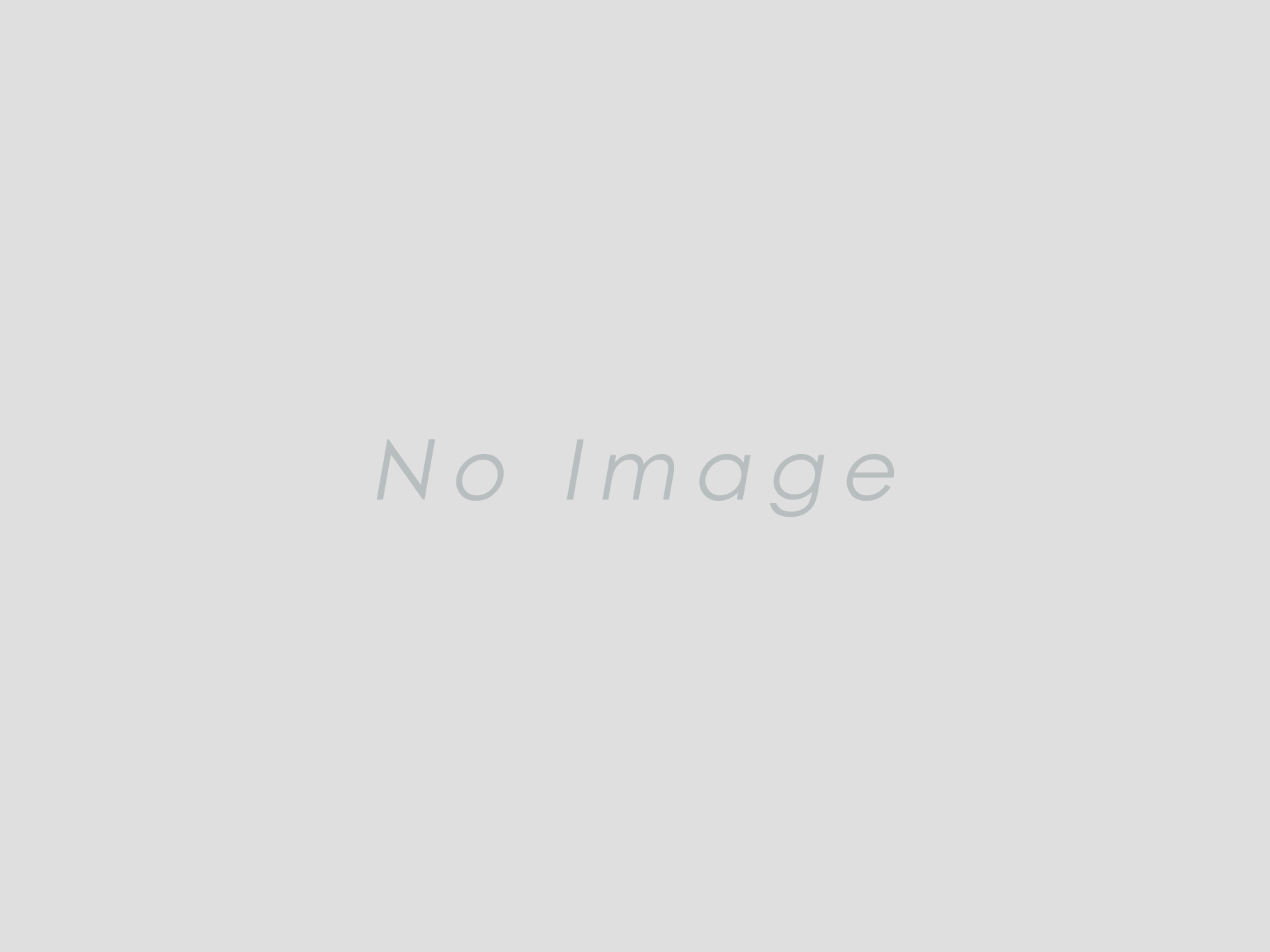
効率化を図る材料選定の要点
精密加工において効率化を図るための材料選定は、非常に重要なステップです。加工の効率を左右する要素には、材料の機械的特性、耐久性、そして加工適性が含まれます。例えば、アルミニウムやチタンといった軽量かつ強度の高い材料は、高速加工を可能にし、生産性の向上に寄与します。また、材料の選定に際しては、熱膨張係数や化学的安定性といった特性も考慮されます。このような特性を理解し適切に選定することで、加工の効率を最大限に引き出すことが可能になります。特に、精密加工では短納期での量産が求められるため、材料選びの段階で効率化を意識することが、競争力を保持する上で欠かせません。
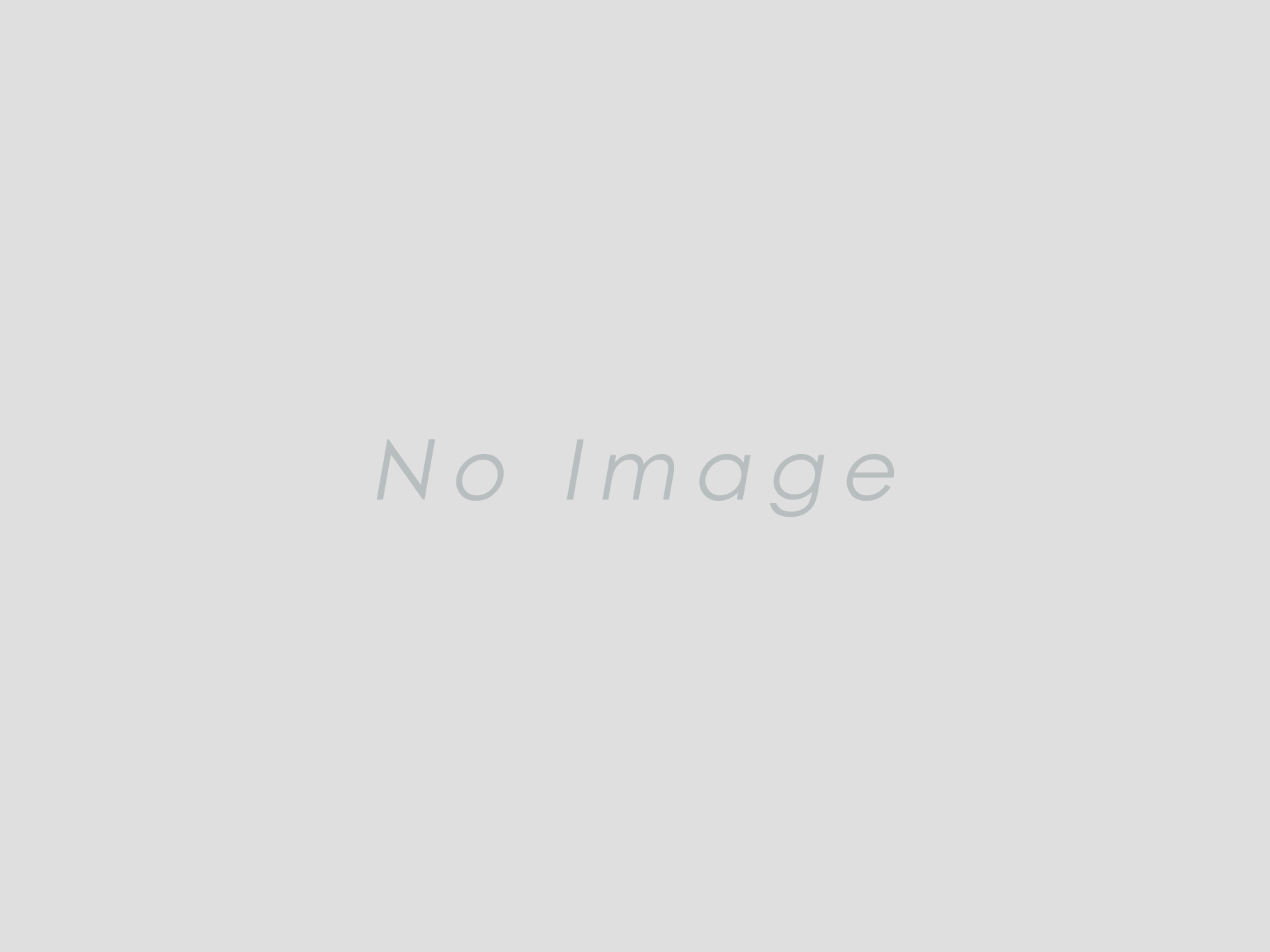
加工時間短縮に寄与する材質の特性
精密加工において加工時間を短縮するためには、材質の選定が直接的な影響を及ぼします。特に、硬度が高く熱伝導性に優れた材質は、加工時の摩擦熱を効率的に逃がし、加工速度を向上させることができます。また、加工中に変形しにくい安定した材質を選ぶことも重要です。これにより、工具の摩耗を抑え、加工精度を保つことが可能になります。例えば、セラミックスや高強度鋼は、こうした加工特性を備えており、特に高精度かつ高速な加工が求められる場面で重宝されます。加工時間の短縮は、コスト削減に直結するため、材料の特性を理解し活用することが、効率的な精密加工の実現に不可欠です。
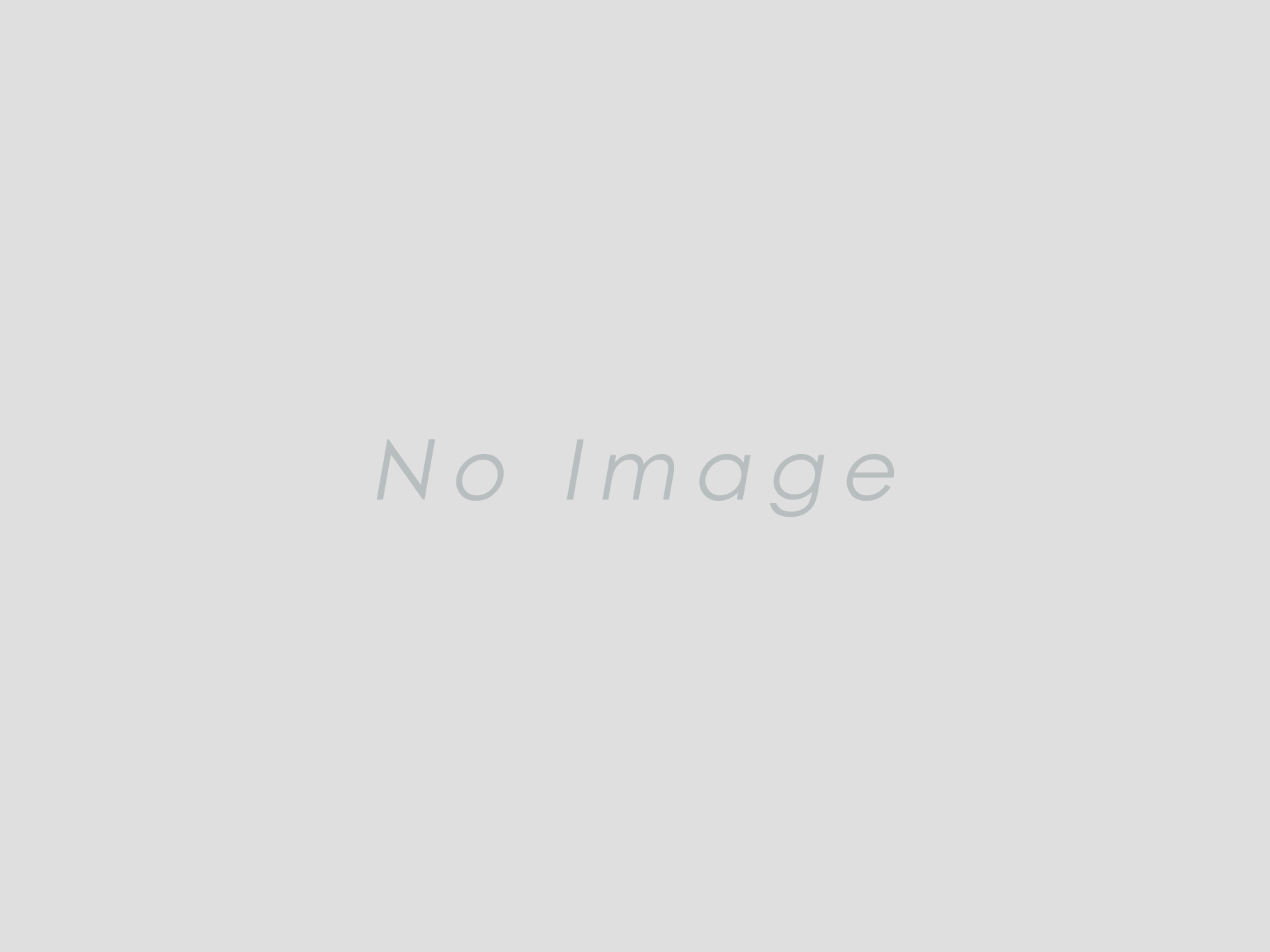
工具寿命を延ばす材質の選び方
精密加工において、工具の寿命を延ばす材質の選択は、加工の効率性と経済性に直結します。特に、耐摩耗性に優れた材質を選ぶことが重要です。高速度鋼(HSS)や超硬合金は、耐久性と摩耗抵抗性に優れ、多くの加工現場で活用されています。これらの材質は高速切削にも対応可能で、長時間の加工においても優れた性能を発揮します。また、チタンアルミナイト(TiAlN)やダイヤモンドライクカーボン(DLC)などのコーティングは、摩擦や熱に強く、工具の劣化を抑制します。このような寿命を延ばすための選択は、工具の交換頻度を減らし、結果的にコスト削減につながります。
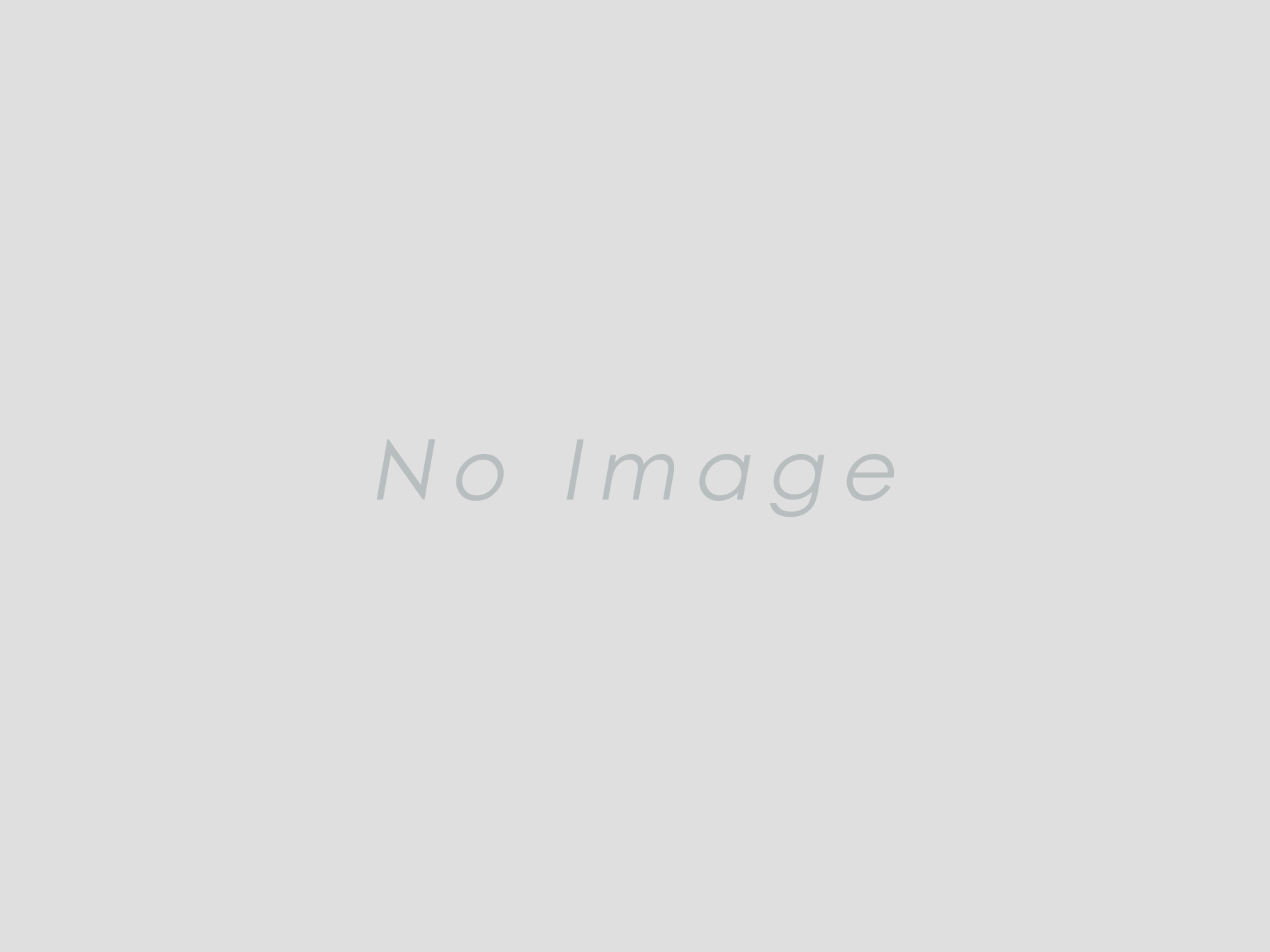
加工精度を向上させる最適な材質
精密加工において、加工精度を向上させるためには、適切な材質選びが欠かせません。高精度な製品を実現するためには、寸法安定性を持つ材質が求められます。例えば、航空機や医療機器の分野では、軽量でありながら強度の高いチタンやアルミニウムが選ばれることが多いです。これらの材質は、熱膨張率が低く、加工中の変形を最小限に抑えることが可能です。また、ステンレス鋼やインコネルなどの耐熱性や耐腐食性を持つ材質も、過酷な環境下における精密加工には最適です。こうした選択により、加工の効率化と製品品質の向上が実現します。
精密加工の品質向上に繋がる材質とは
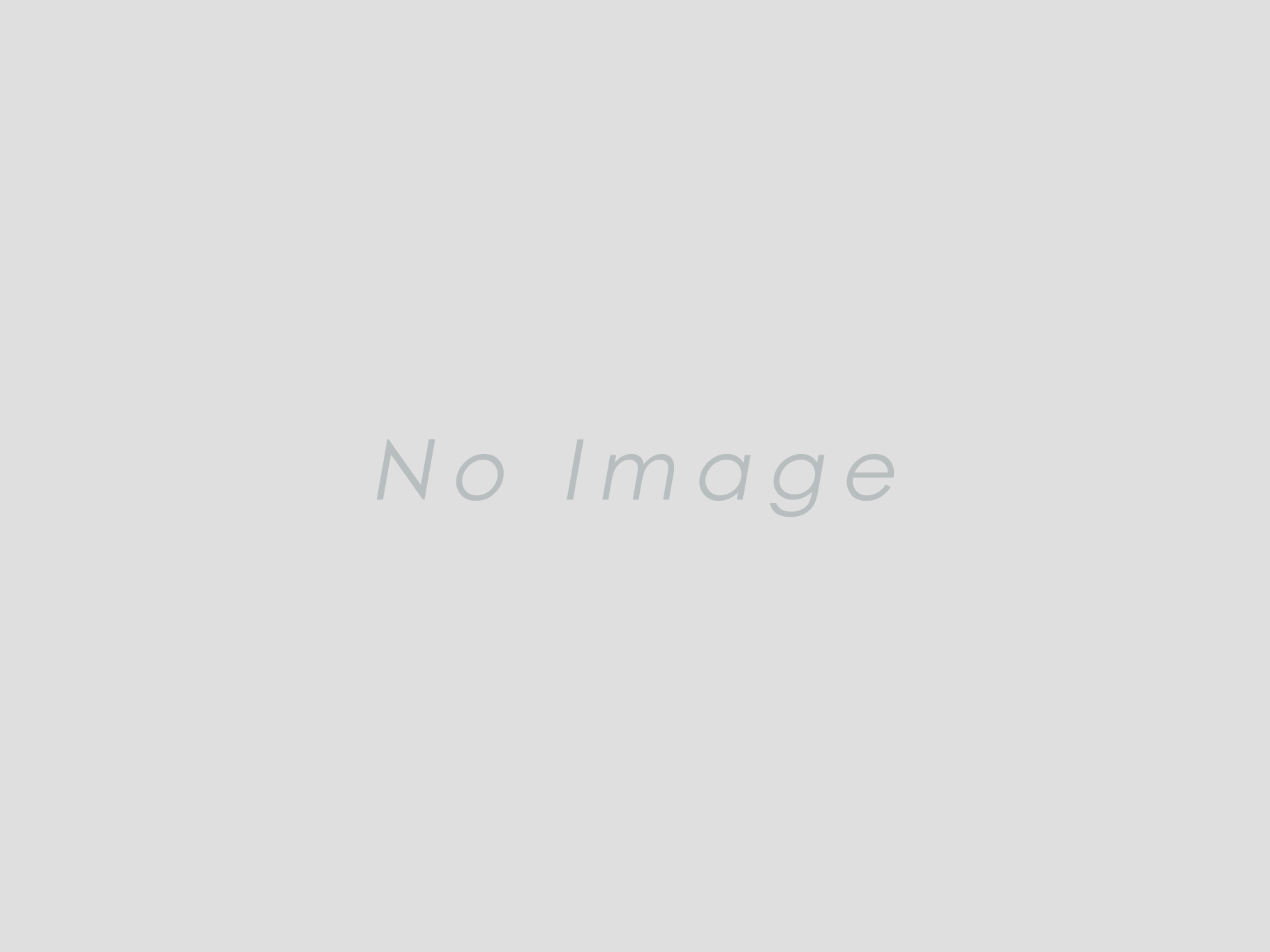
高品質を実現する材質の要素
精密加工において高品質な製品を実現するためには、使用する材質の特性を深く理解し、適切に選ぶことが重要です。まず、引張強度や耐久性は多くの産業で求められる基本的な要素です。特に航空機や自動車産業では、軽量かつ高強度な材質が必要とされ、チタンやアルミニウム合金がその要件を満たします。また、熱膨張係数の低さも重要であり、温度変化に対する寸法安定性が求められる場面では、素材選びが製品の精度に直結します。さらに、耐腐食性も考慮しなければなりません。ステンレス鋼やニッケル合金は、腐食環境下でも優れた性能を発揮するため、医療機器や食品加工装置で多く使用されています。最適な材質選びは、製品の性能を最大限に引き出し、結果的に高品質を実現する鍵となります。
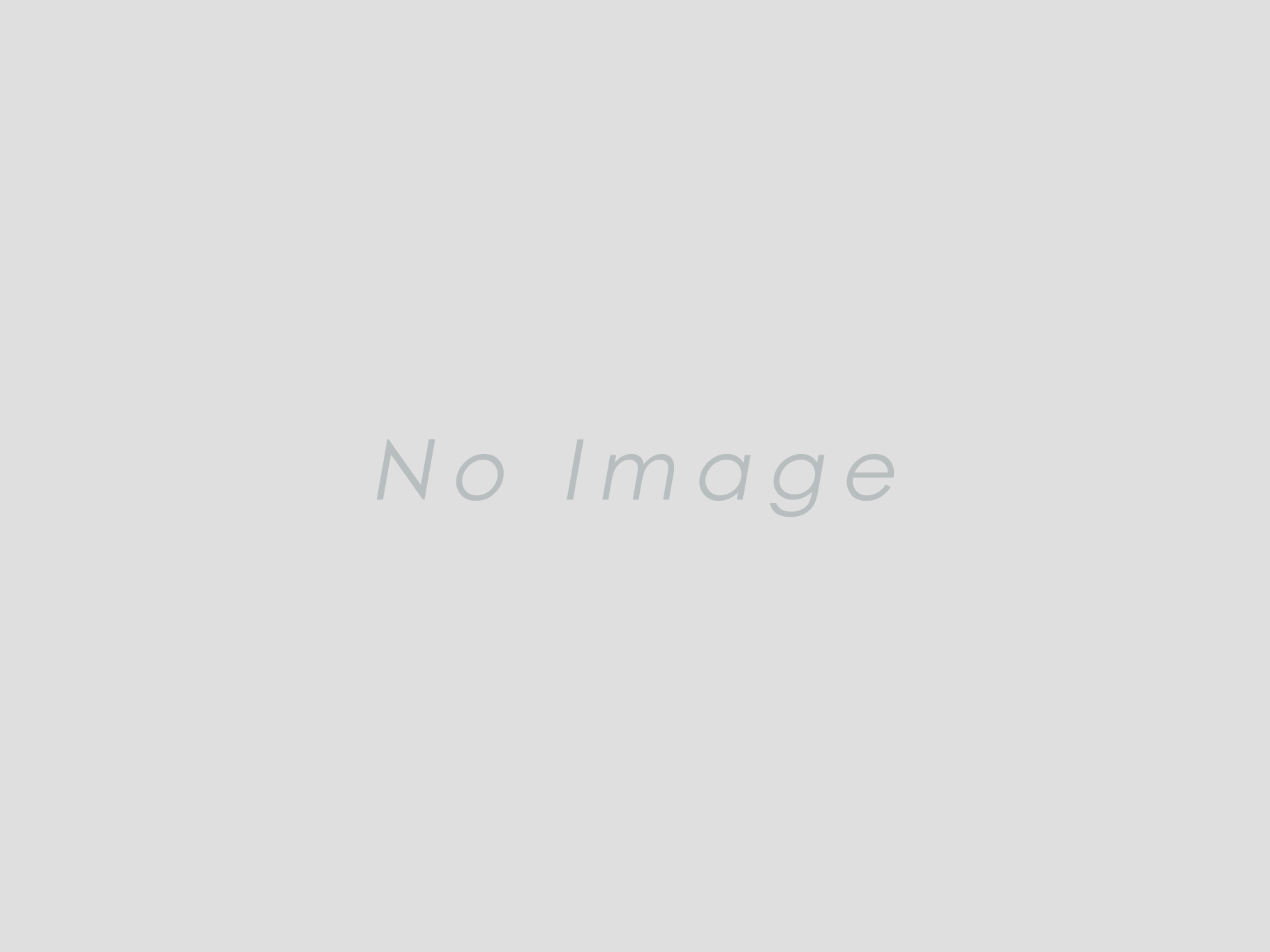
材質選びが品質管理に与える影響
精密加工における材質選びは、製品の品質管理に直接的な影響を及ぼします。まず、素材の均質性が重要です。均質性の高い素材を使用すれば、製品の一貫した品質を保つことができ、不良品率を低下させることが可能です。特に、大量生産される製品では、わずかな材質の不均一が多大な影響を及ぼすことがあります。また、材質の選定は製品の検査プロセスにも影響を与えます。例えば、加工中の寸法安定性が優れている材質を選べば、検査工程での手間を軽減することができます。さらに、適切な材質選びは、生産ライン全体の効率を向上させる要因となり、企業のコスト削減にも寄与します。品質管理において材質選びが果たす役割は非常に大きく、これを疎かにすることはできません。
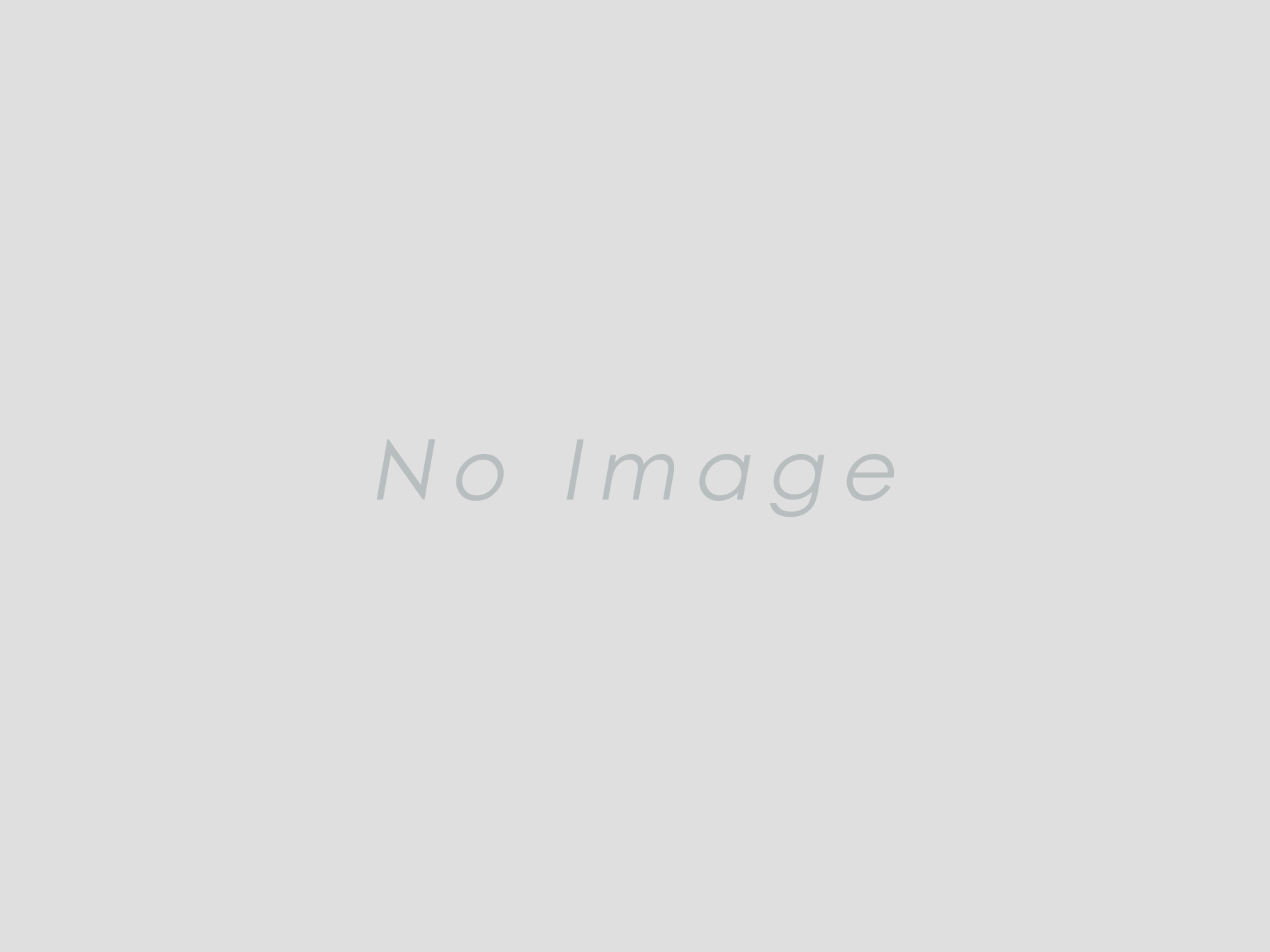
加工後の製品精度を左右する材質選定
精密加工において、加工後の製品精度を保つためには、材質選定が極めて重要です。加工中に寸法の変動を最小限に抑えるためには、特定の温度範囲で形状が安定する材料を選ぶことが求められます。例えば、耐熱性や熱膨張係数の低い材料は、加工時の熱変形を抑制し、高精度を維持するのに適しています。また、材料の硬度と弾性率も重要な要素で、これらが加工精度に直結します。硬度が適切でない場合、工具の摩耗が激しくなり、結果として加工精度が低下する危険性があります。このため、加工対象の用途や環境条件を十分に考慮し、材料選定を行うことが求められます。そして、最適な材質選びが、製品の信頼性と性能を大幅に向上させる鍵となります。
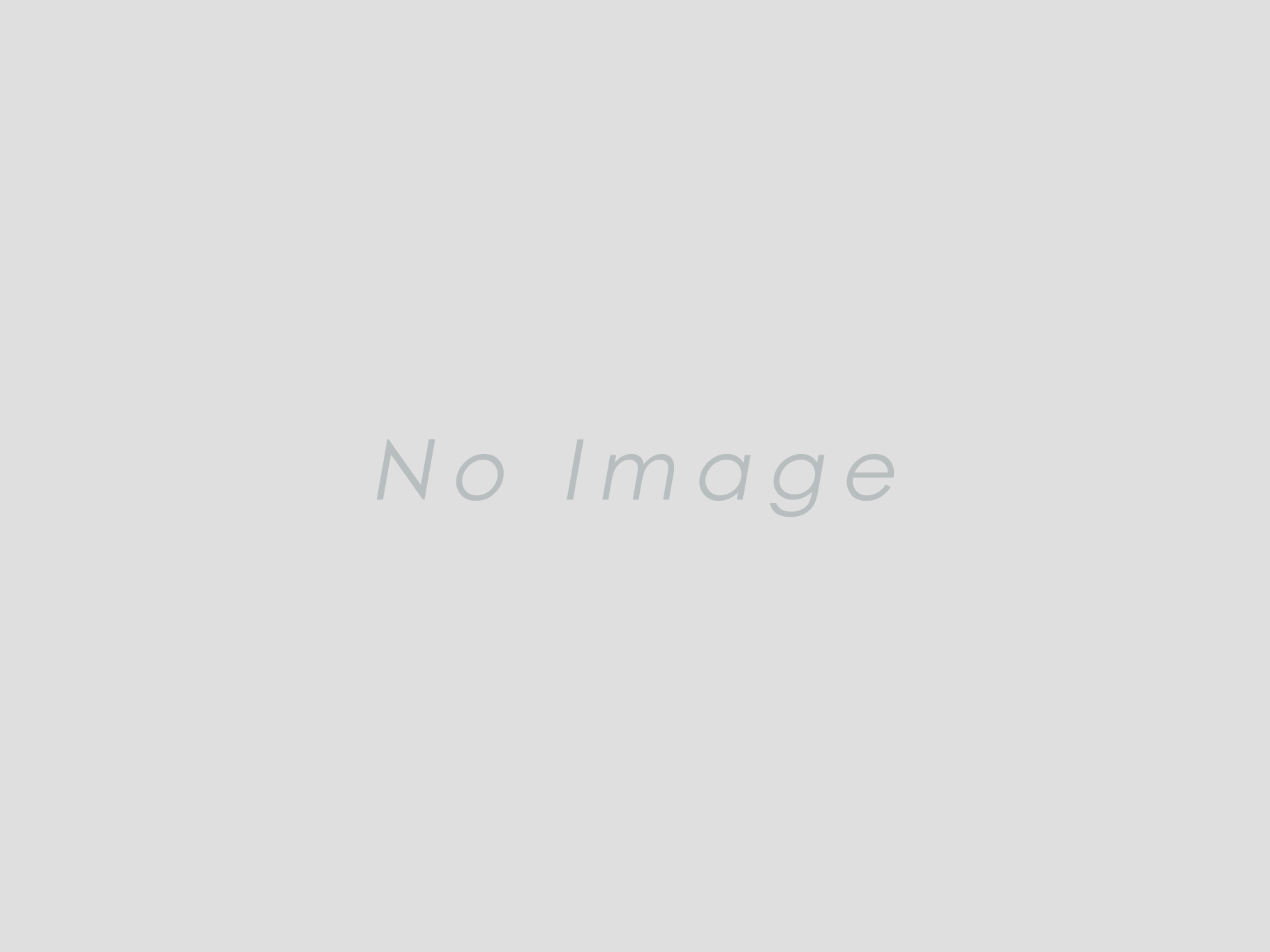
不良品率を低下させる材料戦略
精密加工における不良品率を低下させるための材料戦略は、製品の品質を大きく左右します。まず、材料の均質性が高いことが求められ、これにより加工中のばらつきを抑えることができます。また、素材の切削性も重要で、切削抵抗が低い材料を選ぶことで、加工誤差を最小限に抑えることが可能です。さらに、材料の供給の安定性を確保することも重要で、不安定な供給は加工ラインの停止や品質低下につながる可能性があります。これらの要素を総合的に考慮した材料戦略が、不良品率を下げ、結果として製造コストの削減と品質向上を実現します。正確な加工に適した材料を選択することで、顧客満足度の向上にもつながります。
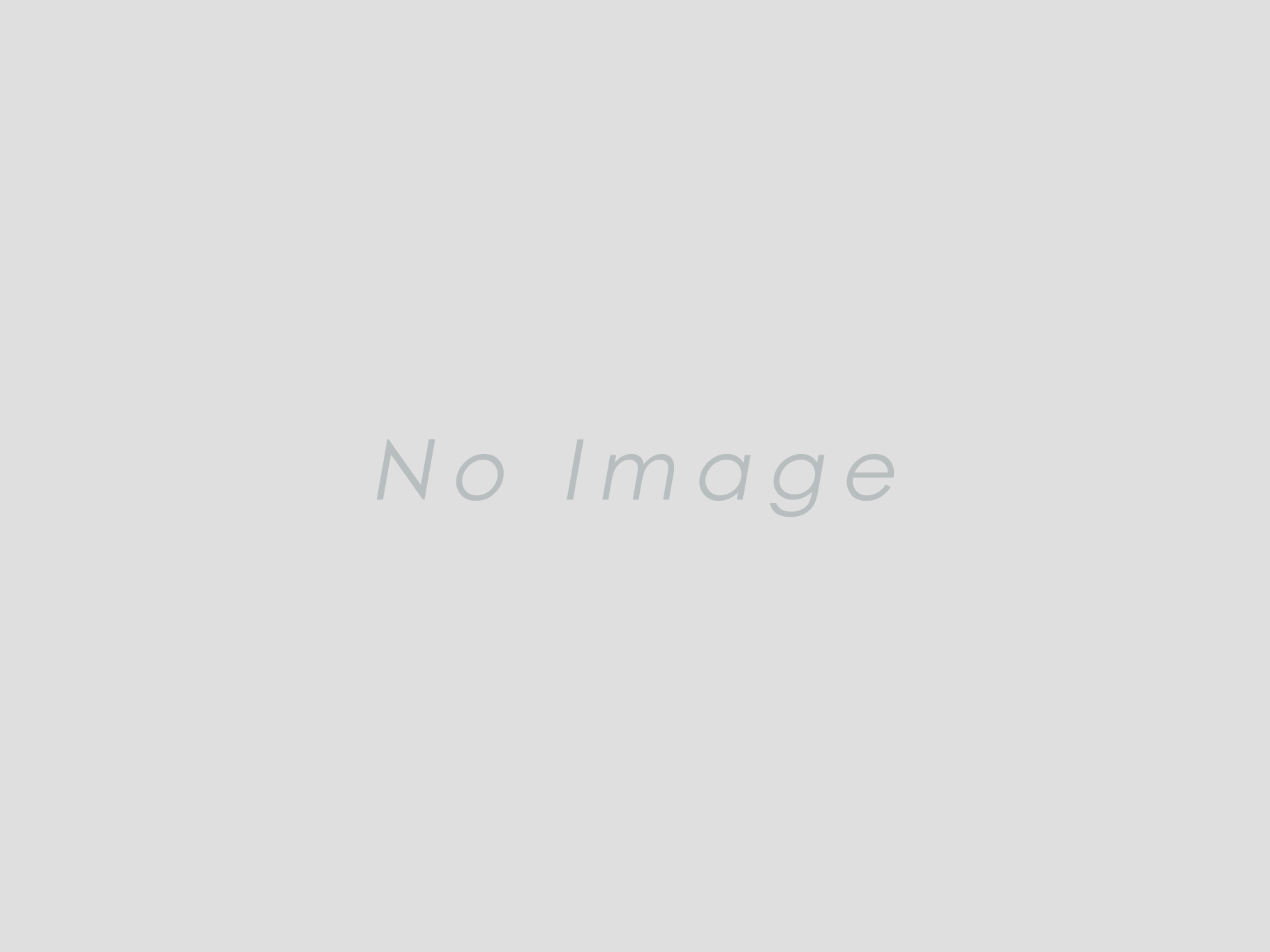
品質保証のための材料選びの基準
精密加工における品質保証は、材質選びから始まります。適切な材質選定は製品の信頼性を確保し、耐久性を向上させる重要な要素です。例えば、耐久性の高い材質を選ぶことで、長期間にわたって高い性能を維持することが可能です。また、材質の化学成分や機械的性質を詳細に検査することで、不良品率を低下させることができます。最新の検査技術を活用し、材質特有の欠陥を早期に発見し是正することも、品質保証の基礎となります。さらに、加工中の寸法安定性や熱伝導性を考慮した材料選びが、製品の高精度を実現します。このように、材質選びは製品の品質を左右する重要なステップであり、精密加工における品質保証の基盤を形成しています。
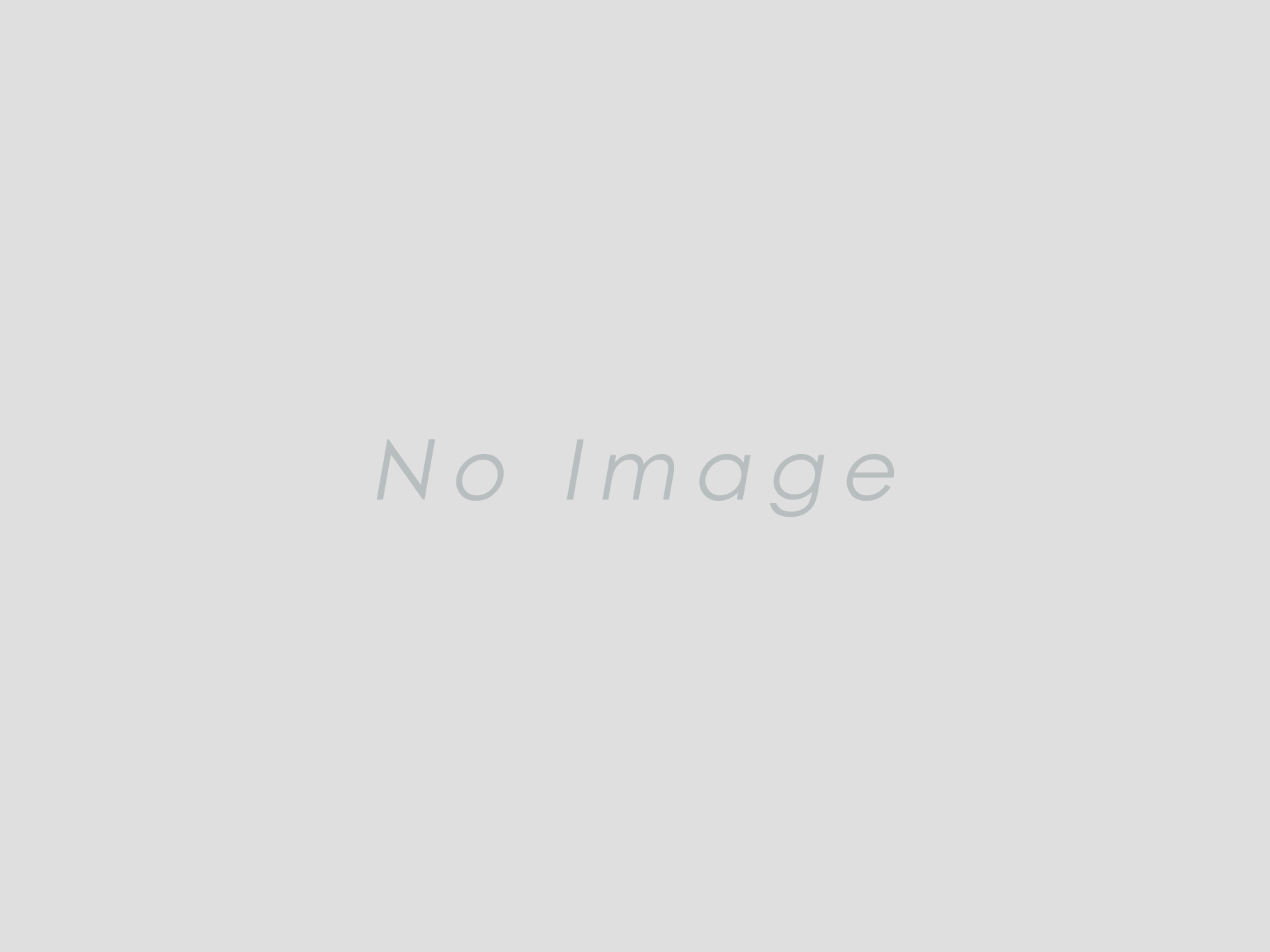
顧客満足度を高める材質の選び方
精密加工において、材質選びは顧客満足度に直結します。適切な材質を選定することで、製品の性能や耐久性が向上し、顧客の期待に応えることができます。例えば、航空機部品では軽量で強度のあるアルミニウムが選ばれることが多く、燃費の向上に寄与します。また、医療機器では耐腐食性の高いチタンが選ばれ、長期間の使用に耐えることが求められます。さらに、材質の選定には環境への配慮も必要で、リサイクル可能な材料を選ぶことで、持続可能な生産が可能になります。顧客のニーズをしっかりと把握し、それに基づいた材質選びを行うことが、長期的な信頼関係を築く鍵となります。質の高い製品を提供することで、顧客満足度を高め、企業の信頼性を向上させることができるのです。
精密加工における寸法安定性の確保と材質選び
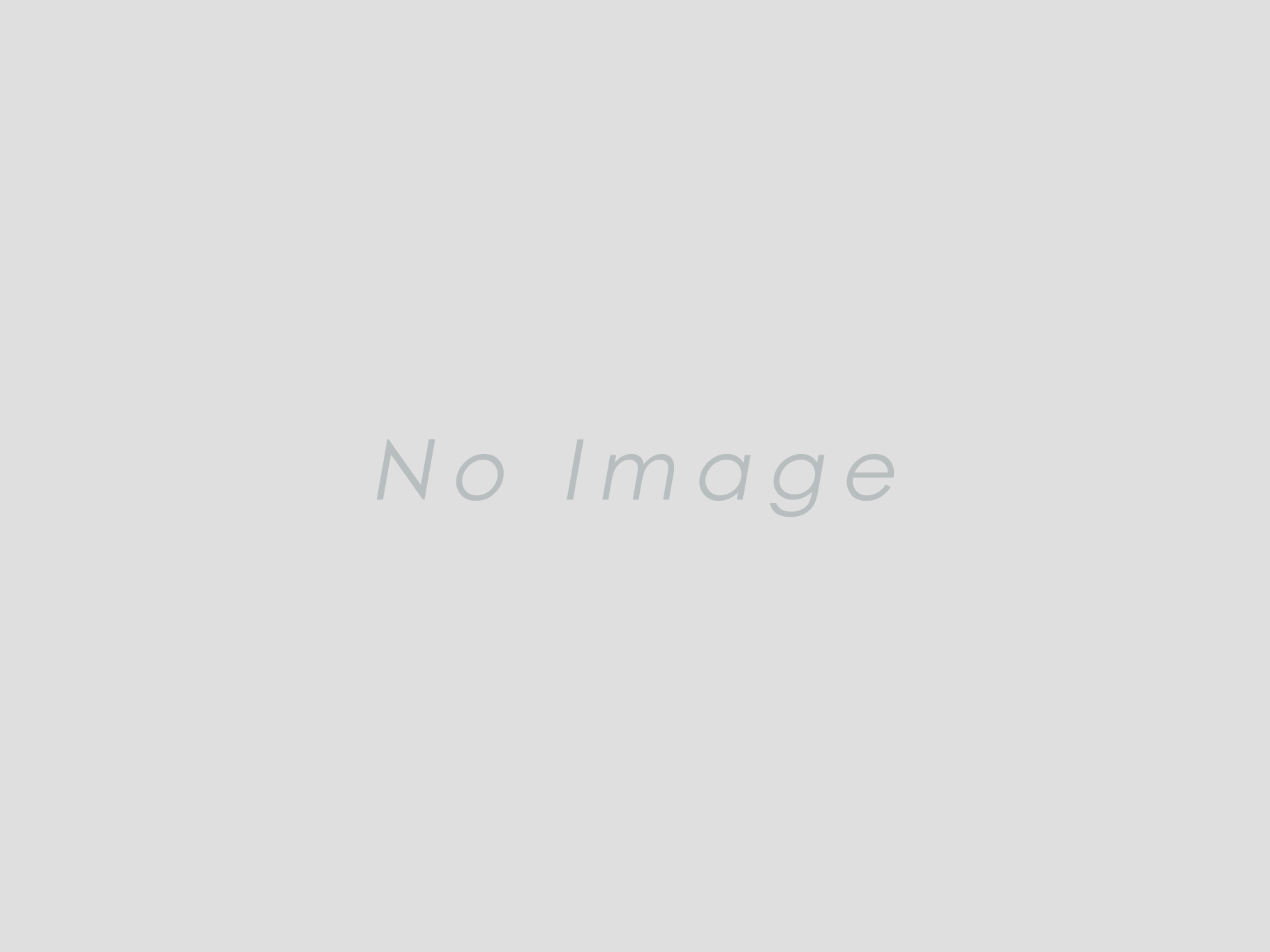
寸法安定性を確保する材料選定法
精密加工において寸法安定性は欠かせない要素です。この安定性を確保するためには、まず材料の熱膨張係数に注目する必要があります。材料が温度変化に対してどれだけ寸法を維持できるかを示すこの係数が低いものを選ぶことで、加工中の変形を最小限に抑えられます。また、硬度が均一であることも重要であり、材料内の硬度のばらつきが少ないものを選ぶと加工精度が向上します。ステンレス鋼やアルミニウム合金は、この点で優れた特性を持っており、寸法安定性の確保に貢献します。さらに、熱処理を施すことで、これらの材料の寸法安定性をさらに向上させることが可能です。
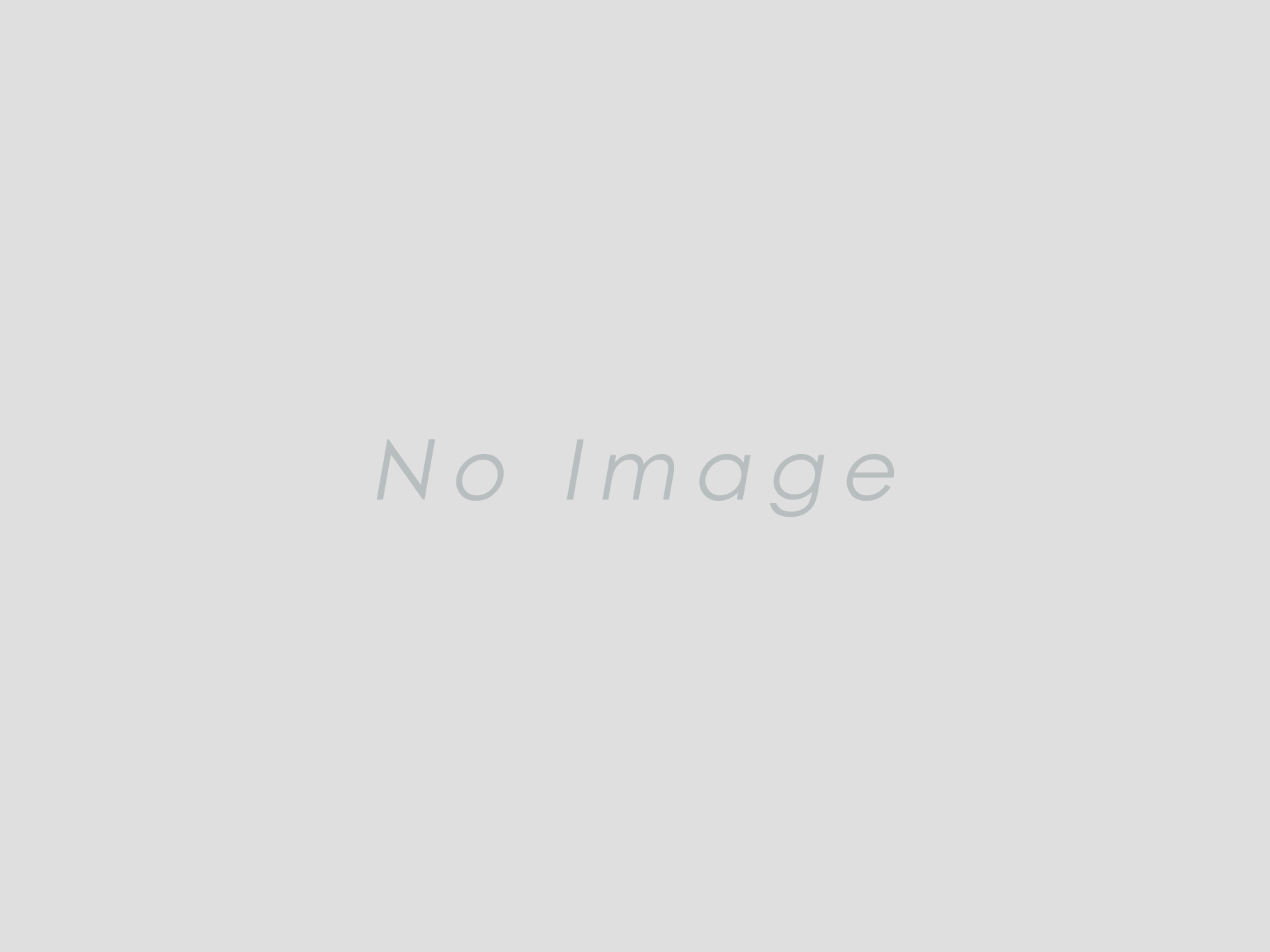
加工中の変形を防ぐ材質の特性
加工中の変形は、精密加工において品質を左右する重大な問題です。この変形を防ぐためには、耐熱性と耐応力性に優れた材料を選ぶことが重要です。例えば、チタン合金は優れた耐熱性と強度を持ち、航空機部品などの高応力環境下での使用に適しています。さらに、加工中の振動を吸収する特性を持つ材料も注目されています。こうした材料は、加工時に発生する微細な振動を抑制し、寸法精度を確保します。また、これらの材料選定は、製品の長寿命化と信頼性向上にも寄与します。最適な材料選定により、加工効率が向上し、コスト削減も期待できます。
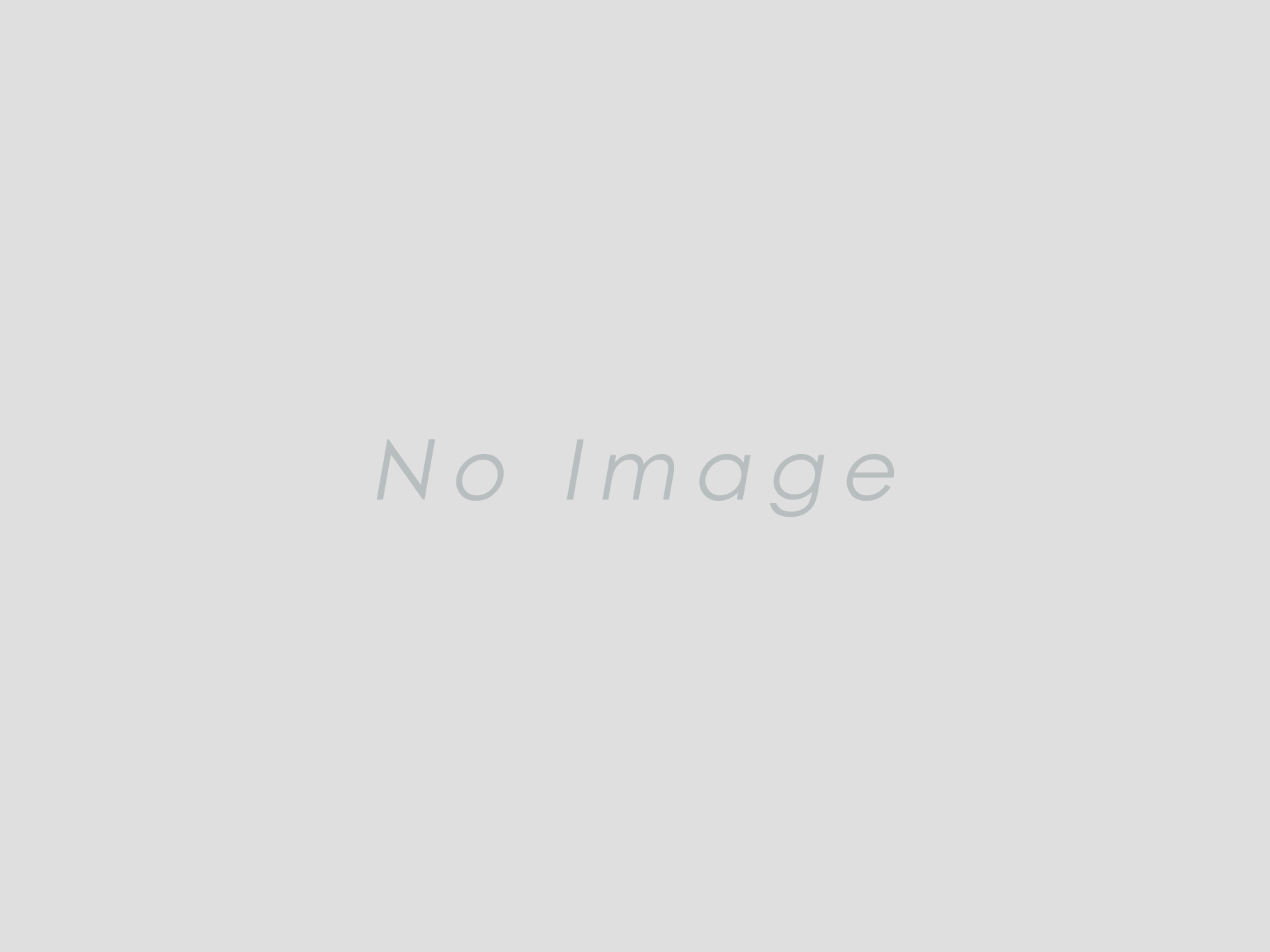
環境変化に強い材料の探求
精密加工における材質選びは、環境変化に対する耐性も重要な要素となります。特に、温度や湿度の変動が頻繁に起こる環境では、材質選定が製品の品質に大きく影響します。例えば、温度変化に敏感な製品には、熱膨張係数が低く寸法安定性に優れた材料が適しています。一方、湿度変化に強い材料としては、吸湿性の低い樹脂や耐腐食性のある金属が考えられます。さらに、化学物質に曝露される可能性のある環境では、耐薬品性の高い材料が必要です。このように、使用環境を考慮した材質選定は、製品の耐久性と信頼性を高めるために欠かせません。
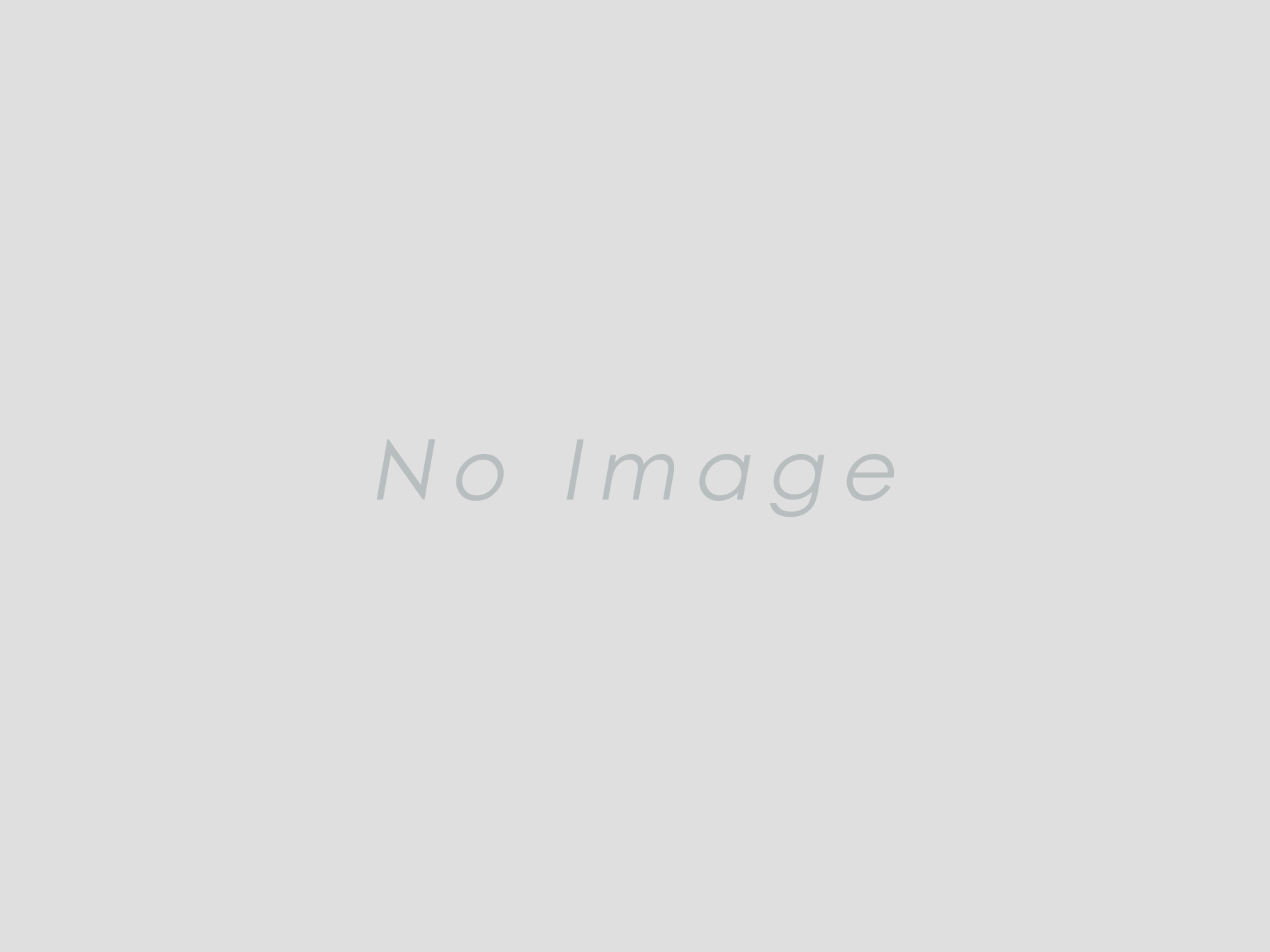
寸法誤差を最小限に抑える材質
精密加工において、寸法誤差を最小限に抑えることは、製品の性能と品質を保証するために不可欠です。このためには、加工中の変形を防ぐための適切な材質選びが重要です。例えば、加工中に熱が発生する場合、熱伝導性が高く、熱膨張係数が低い材料を選ぶことで、寸法変化を抑制できます。また、機械的な衝撃や振動に対しても、弾性に優れた材料が推奨されます。チタンや高合金鋼は、その強度と寸法安定性で知られており、精密加工において広く利用されています。加工精度を維持するためには、材料の特性を深く理解し、それに基づいた選定が求められます。
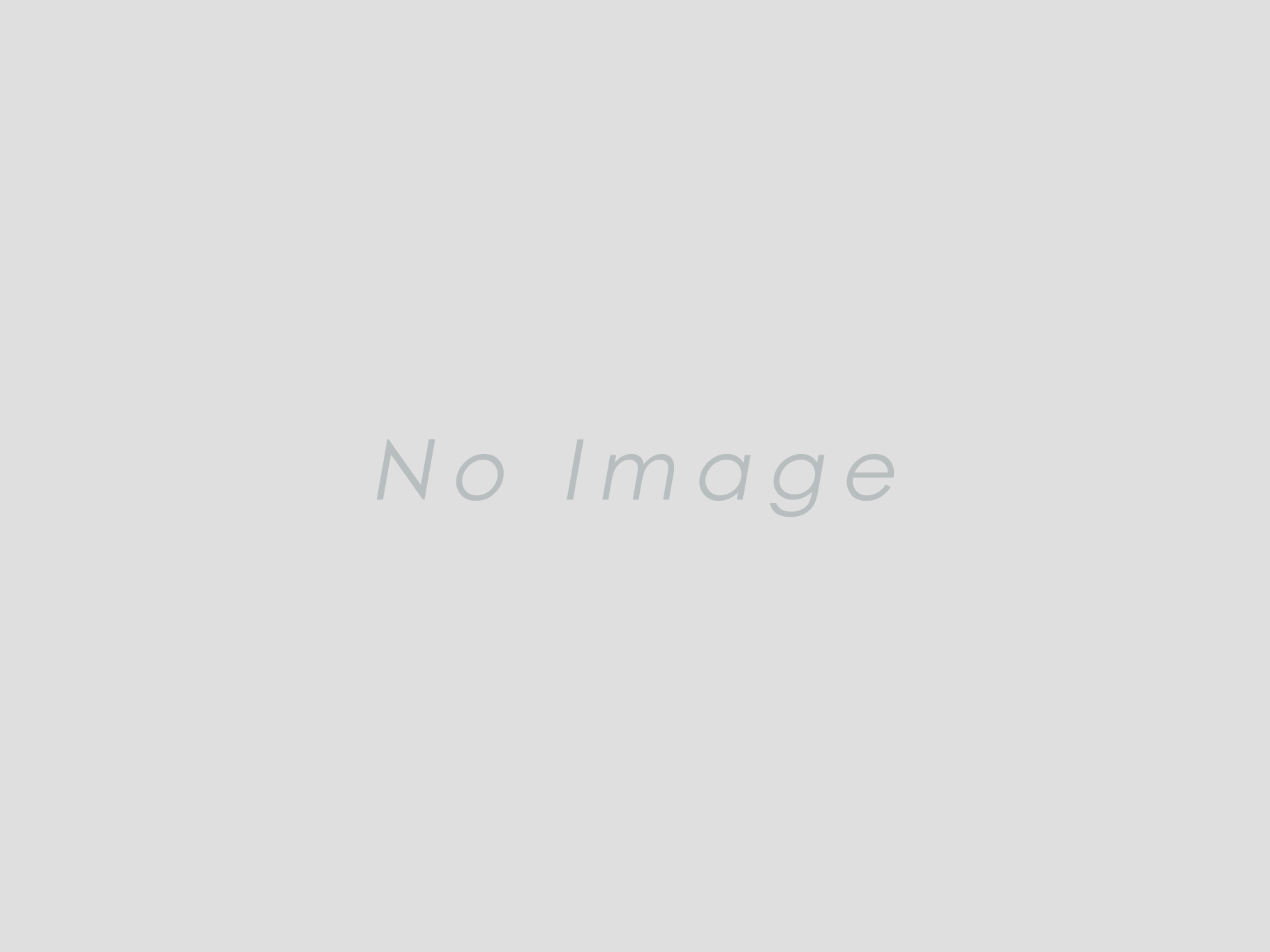
加工精度の維持に貢献する材料
加工精度を高めるためには、選定する材料の特性が非常に重要です。材料の硬度や熱膨張係数、耐摩耗性は、加工中の精度維持に大きな影響を与えます。特に、温度変化が激しい作業環境では、寸法変動が生じやすいため、熱膨張が小さい材料を選ぶことが推奨されます。例えば、インバーやコバールなどの低熱膨張合金は、寸法安定性を保つのに適しており、精密加工で高精度を維持するための選択肢として重宝されています。また、材料の耐摩耗性も考慮することで、工具の寿命を延ばし、安定した加工を実現できます。これらの要素を総合的に判断し、最適な材料を選定することで、加工精度を高水準で維持することが可能となります。
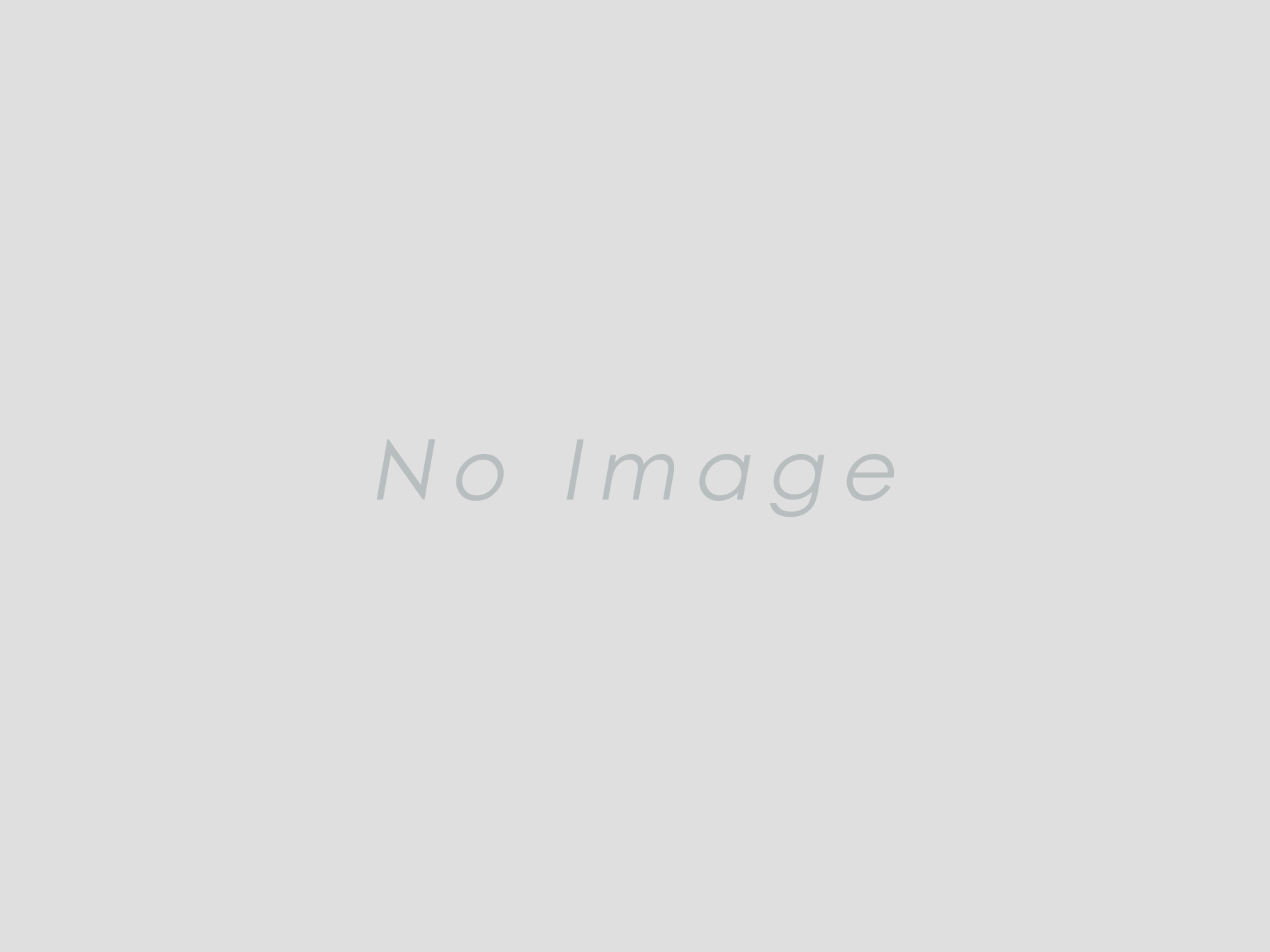
寸法管理が求められる製品への対応
寸法管理が厳しく求められる製品の製造では、材料選定が成功への鍵となります。例えば、航空機部品や医療機器などでは、寸法誤差が許容されないため、加工中の変形を最小限に抑える材料が求められます。こうした要求に応えるためには、加工環境に対する耐性が高く、寸法安定性が優れた材料を選ぶことが重要です。特に、チタンやアルミニウムは軽量でありながら強度が高く、寸法安定性が良好であるため、精密加工において頻繁に使用されます。さらに、これらの材料は耐腐食性にも優れ、長期にわたり製品の品質を維持することが可能です。このように、適切な材料選定は、寸法管理が求められる製品における加工精度の維持と品質の向上に貢献します。
精密加工における最適な材質選びの結論
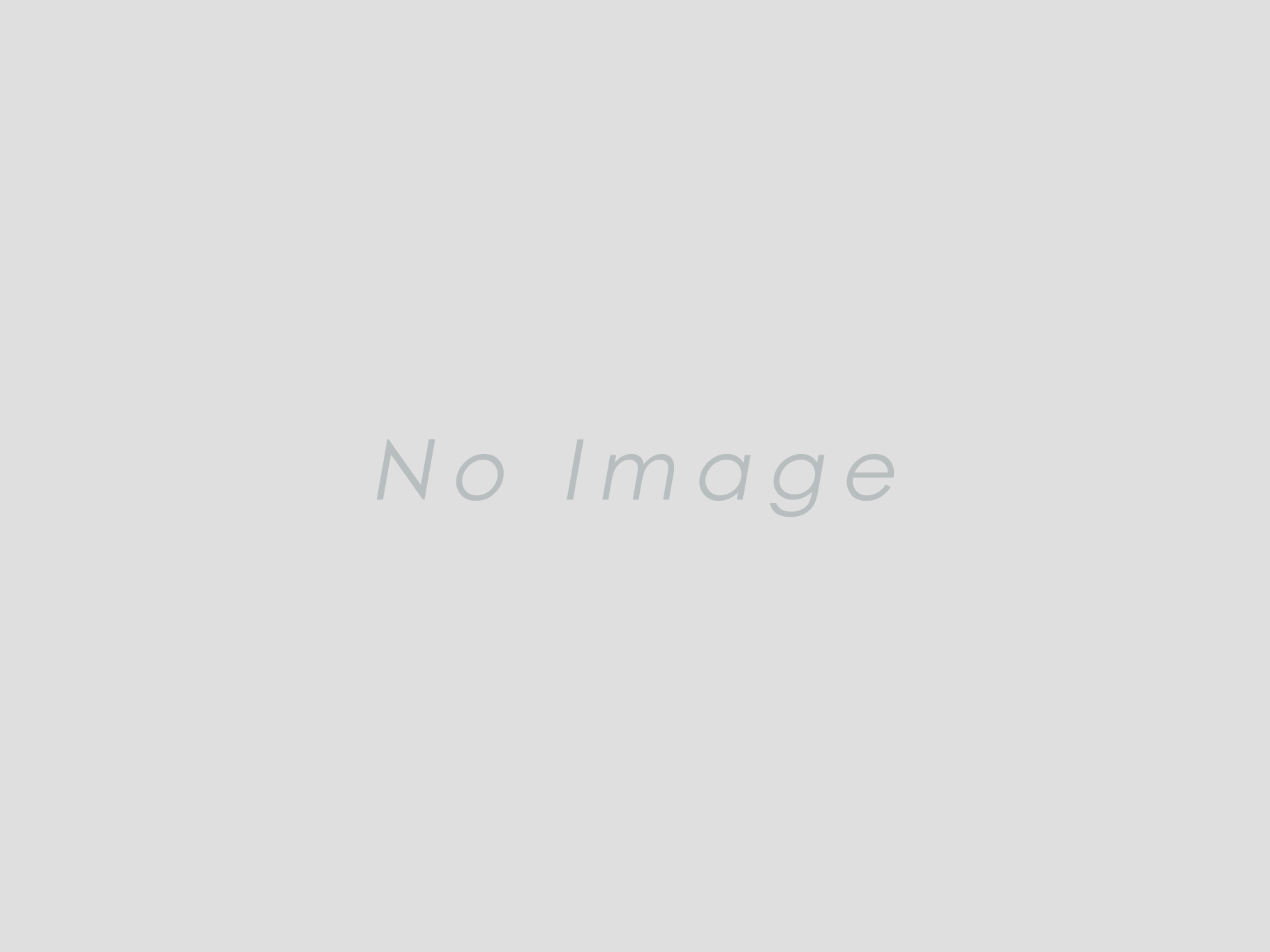
最適な材質選びを導くプロセス
精密加工において最適な材質を選ぶためには、まず使用目的と加工環境を明確にすることが重要です。具体的には、製品が使用される条件や要求される特性をリストアップし、それに基づいて適した材質を絞り込みます。例えば、耐久性が求められる場合は、硬度の高い鋼材やセラミックが適していますが、軽量性が重要ならチタンやアルミニウムが選ばれることが多いです。次に、各候補材の加工性を評価し、実際の加工工程での効率を考慮します。さらに、材料の供給業者の信頼性とコストも検討することで、全体のプロセスを最適化します。この一連のプロセスを標準化することで、効率的かつ安定した精密加工が可能になります。
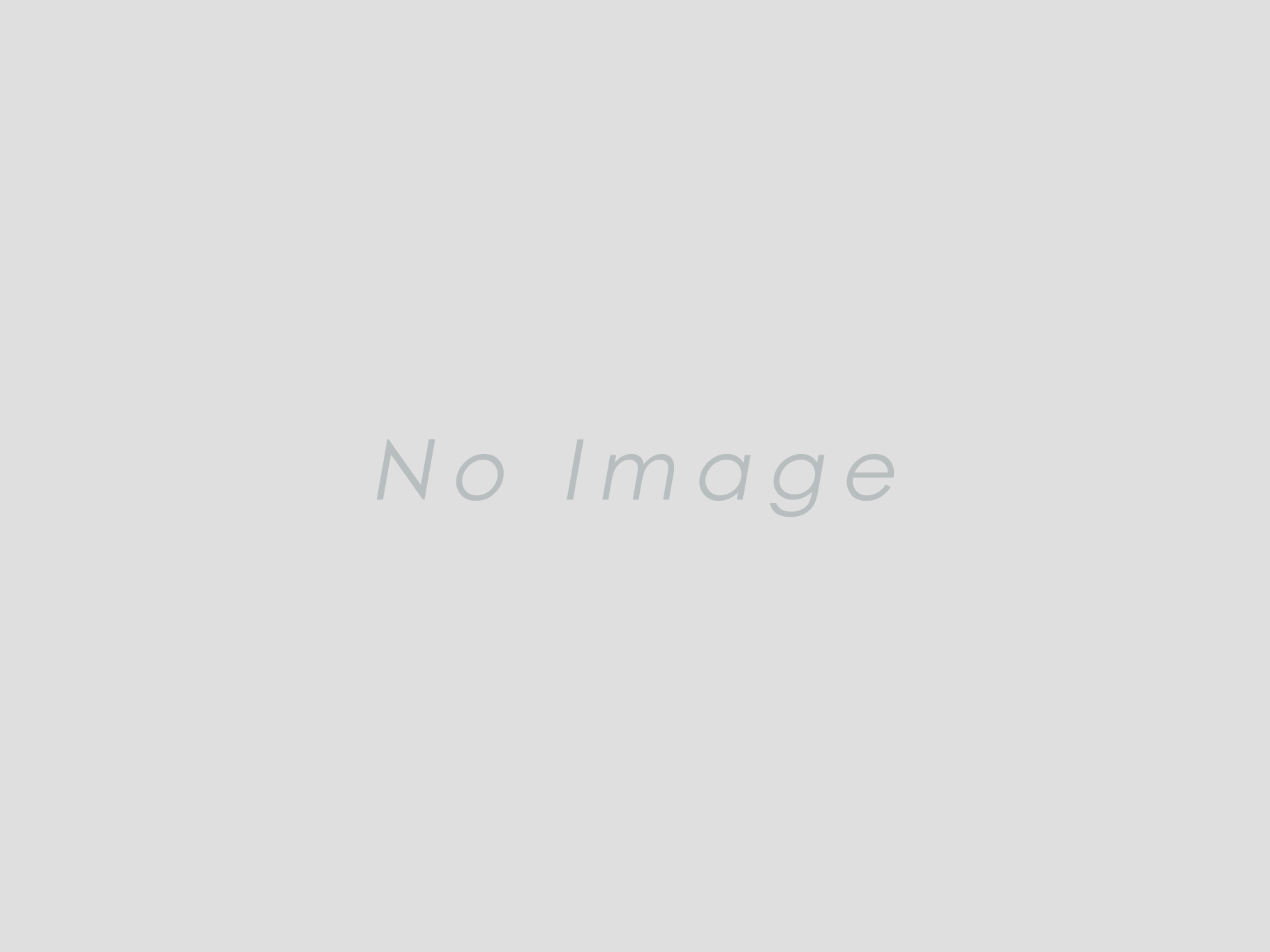
材質選定の成功事例とその分析
精密加工の分野では、材質選定が製品の品質と性能に直結します。例えば、ある航空機部品メーカーでは、チタンを使用することで軽量化を達成し、燃費を向上させることに成功しました。この選択は、材質の耐久性と加工のしやすさを両立するためのものでした。また、医療機器の分野でも、耐腐食性が求められる環境でステンレススチールを選ぶことで、長期間の使用に耐えうる製品を提供しました。これらの事例は、使用条件に応じた材質選びの重要性を示しています。成功事例から学ぶことで、他の精密加工分野でも最適な材質選定の可能性を広げることができるでしょう。
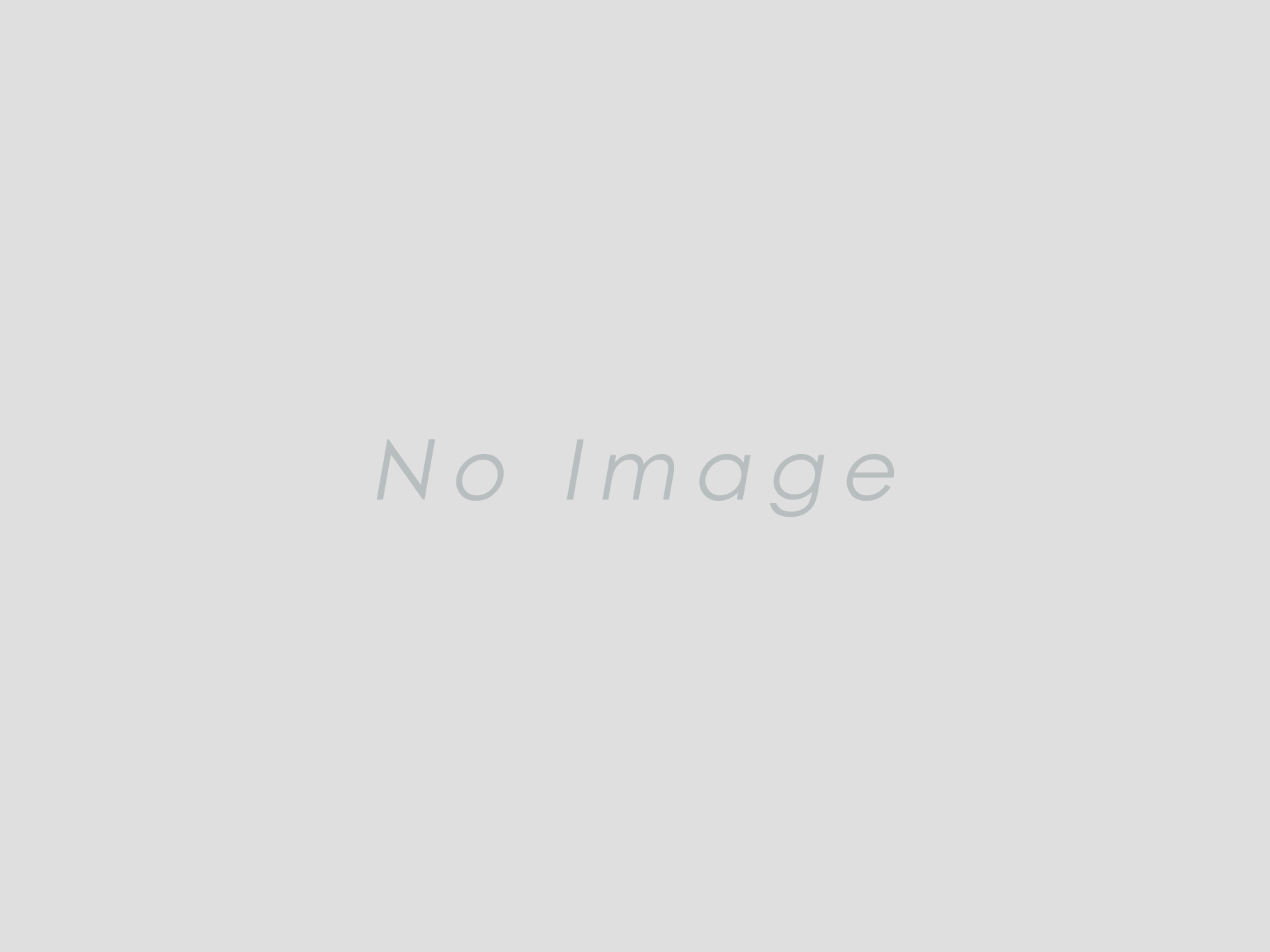
精密加工における材料選びの未来
精密加工における材料選びの未来は、技術革新とともに大きく進化しています。特に、ナノテクノロジーやAIを活用した材料開発が注目されています。これにより、新たな合金や複合材料の特性がより詳細に分析され、加工精度の向上が期待されています。従来の材料では達成できなかった高い耐久性や軽量化が可能となり、航空宇宙や医療分野における精密加工の可能性が広がります。また、持続可能な材料の開発も進んでおり、リサイクル可能な合金やバイオプラスチックなど環境に配慮した選択肢が増えています。これらの新素材は、企業の製品戦略において重要な役割を果たし、競争力を高める要素となります。
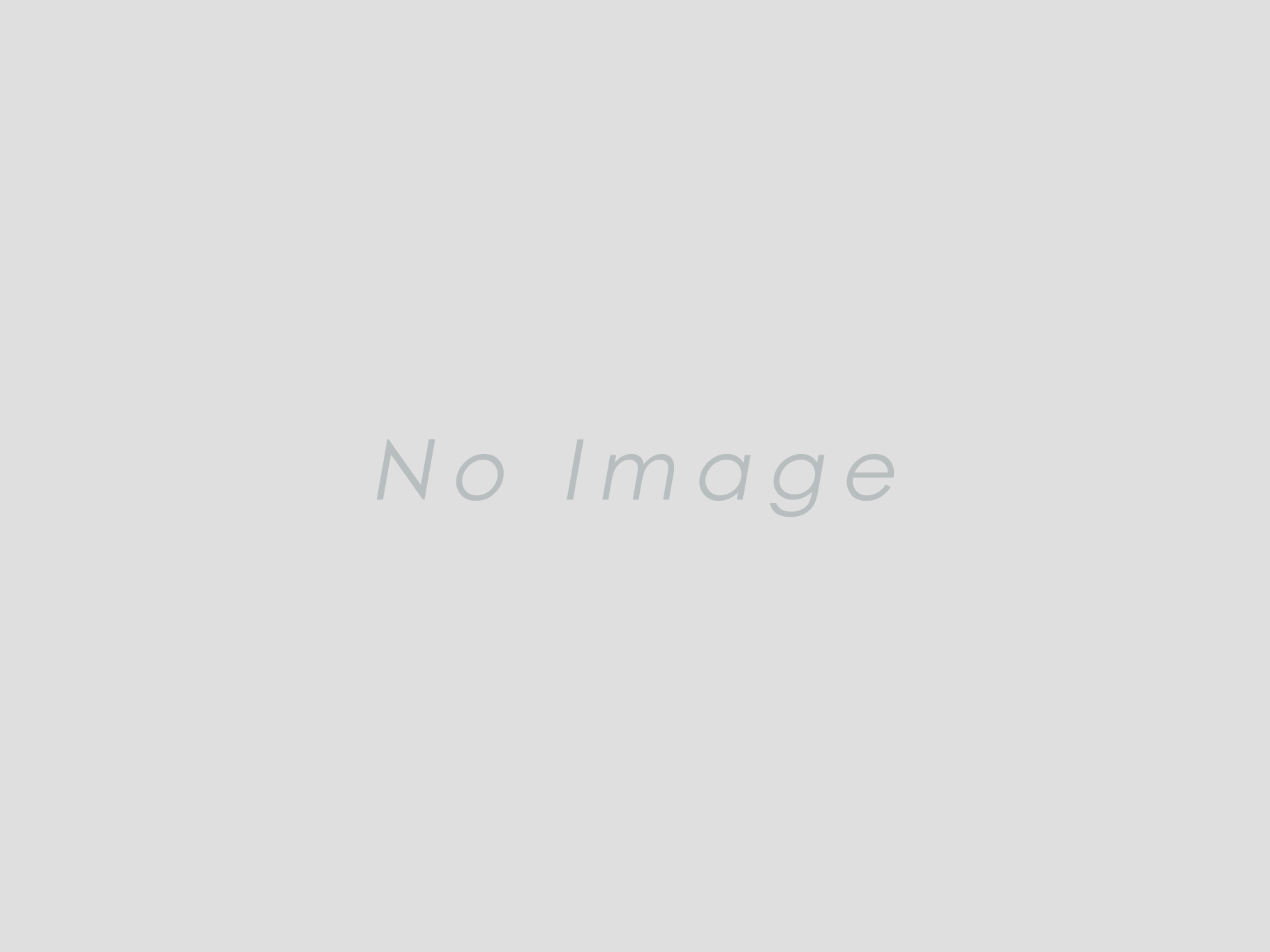
持続可能な材料選択への取り組み
持続可能な材料選択は、精密加工業界における最重要課題の一つです。環境負荷を軽減するための取組みとして、リサイクル素材や再生可能エネルギーの利用が進んでいます。これにより、生産コストの低減とカーボンフットプリントの削減が可能となります。また、企業間での共通プラットフォームを利用した材料データの共有が推奨されており、効率的な選定プロセスが実現されつつあります。特に、バイオマス由来の新素材や環境に優しいコーティング技術は、持続可能な加工におけるキーワードとなっています。これらの材料選択と加工技術の組み合わせは、企業の社会的責任を果たすだけでなく、消費者からの信頼を獲得する大きな要因ともなります。